-
The mechanical properties of silty sands are challenging to satisfy the engineering requirements in most underground engineering. As a mature industrial product, cement is widely used to enhance these problematic soils' impermeability and mechanical properties[1, 2]. However, excessive cement consumption in practical engineering may lead to excessive volume shrinkage due to water evaporation during cement soil hardening and consequent shrinkage cracking[3, 4]. Searching for soil improvement methods with ideal performance and environmental-friendly merits has always been a hot topic in academia and engineering[5, 6]. Geopolymer is a dense gelatinized mineral polymer. It commonly originates from the condensation polymerization of activated silicon aluminate minerals in an alkali environment[7, 8]. Geopolymer binders have outstanding performance, including early strength, fast solidification, high volume stability, low permeability, metal ion immobilization, and chemical corrosion resistance. They also possess the characteristics of rich raw materials (most of them are solid waste with high content of silicon and aluminum minerals, such as steel slag, fly ash, red mud, waste glass, and tailings), almost costless, simple to process, and energy efficient[9−11]. If they were used for soil stabilization, their high natural strength and low shrinkage could reduce the shrinkage and crack of the soil, and their good compactness and impermeability could improve the water stability of the soil. Therefore, applying geopolymer in silty sand stabilization could be an effective method for engineering treatment[12]. However, their properties are not inherent in raw materials (mainly blast furnace slag, fly ash, red mud, and metakaolin, etc.) but obtained through adding a suitable alkaline activator, the proportioning of alkaline activator to raw materials and appropriate content[3, 12].
Many scholars have conducted extensive experimental research on geopolymer binders and their application in soil stabilization. In terms of geopolymer activators, Davidovits[11] pointed out that the combination of NaOH or KOH and Na2SiO3 or K2SiO3 was suitable for the alkaline activators. Askarian et al.[13] prepared a single-component geopolymer with Na2SiO3, Ca(OH)2, Na2O, LiOH, K2CO3, and their combinations. Ana María et al.[14] and Wongkeo et al.[15] investigated geopolymer synthesis using strong alkaline and silicate as alkaline activators. For the proportioning of geopolymer precursor and activator, Ong et al.[16] studied the fly ash-based geopolymer synthesis by a low alkali activator content and cold-pressing technique under room temperature. Wang
et al. [8] reported that the ideal proportion of metakaolin, Na2SiO3, and CaO for synthesizing geopolymer was 3.6:1.0:0.8. Chen et al.[17] addressed the synthesis of geopolymer composite from shell coal gasification fly ash and steel slag. For soil stabilization with geopolymer binders, Ding et al. [18] found that the peak load and fracture performance of geopolymer concrete increased with slag/fly ash content and decreased with the ratio of water to the binder. Ghadir & Ranjbar[19] revealed that the compressive strength of clay could reach the peak value when the content of volcanic ash-based geopolymer was 15%. Wang et al.[20] found that the optimum content of metakaolin-based geopolymer in clay was 12% to 15%. For investigating their strengthening mechanism, Guo & Pan[21] found that the early strength of fly-ash steel slag-based geopolymers showed an upward trend since both sodium aluminosilicate hydrate gel and calcium aluminosilicate hydrate gel was formed. However, the excessive steel slag might result in a lower strength increase due to the sample's degree of carbonization. Ooi et al.[22] pointed out that the products of high calcium fly ash-based geopolymers comprised sodium aluminum silicate hydrate and calcium aluminum silicate hydrate gel phases in coexistence. These studies can provide a robust baseline for studying silty sand stabilization with geopolymer binders. To understand the contribution of steel slag-based geopolymer binder on soil stabilization, a series of unconfined compression tests on silty sands with different mixing ratios of material components in the binder and their reasonable mixing ratios were conducted. The optimum mixing ratio of precursor (steel slag) to alkaline activator (the mixture of Na2SiO3 and CaO) and the optimum dosage of steel slag-based geopolymer for silty sand stabilization were explored. The strengthening mechanism of geopolymer-stabilized silty sands was discussed through microstructural images and chemical components observed by SEM and EDS.
-
The testing soil was silty sand collected from the deep pit of the Fengda International Hotel project in Nanjing, China. It was primarily fine round grey-white particles under dry conditions, as shown in Fig. 1. The particle size distributions of this soil were 0.5−1.0 mm: 2.54%, 0.25−0.5 mm: 5.91%, 0.25−0.1 mm: 43.54%, 0.1−0.075 mm: 24.87%, < 0.075 mm: 23.14%. The natural moisture content of the silty sand was 20%, and the maximum and minimum dry densities were 1.726 g/cm3 and 1.208 g/cm3, respectively. The maximum and minimum void ratios were 1.218 and 0.552. The specific gravity was 2.679.
Precursor
-
Steel slag was used as the precursor of geopolymer in this study. Its main components were CaO, SiO2, and Al2O3. Their total mass content was higher than 92%. The specific chemical compositions are shown in Table 1.
Table 1. The chemical compositions of slag.
Component CaO SiO2 MgO Al2O3 Fe2O3 Mass ratio (%) 59.23 29.02 3.89 1.40 6.46 Alkaline activator
-
The combination of Na2SiO3 and CaO was used as the alkaline activator for inducing the polymerization of steel slag. The Na2SiO3 was produced at the Beichen Fangzheng Reagent Factory in Tianjin, China. The CaO was a white powder with more than 95% mineral content, made from Tianjin Beilian Fine Chemicals Development Co., Ltd, China. As shown in Fig. 2, the maximum particle sizes of CaO and Na2SiO3 were 150 mesh (about 0.1 mm) and 0.5 mm, respectively. The silica modulus of Na2SiO3 was 1.0. The water used in specimen preparation was ordinary tap water.
Apparatus
-
The compression tests of geopolymer-stabilized silty sands were conducted by employing a microcomputer-controlled electronic universal testing machine, as shown in Fig. 3a. The maximum loading force of this machine was 20 kN. The constant force and displacement ranges were 0.2%−100%F S (FS is full scale) with an accuracy of ± 0.5%. The loading speed range was 0.001−500 mm/min with a control accuracy of ± 1% (0.001~10 mm/min). When testing, the saturated geopolymer-stabilized silty sand specimens were installed carefully in the middle of the upper and bottom loading plates and initialized the stress and strain records to zero. Then each sample was loaded at a speed of 1 mm/min until apparent failure characteristics appeared, then the loading was stopped manually. The Phenom Pro Scanning Electron Microscope (SEM-JSM-6510) equipped with an Energy Dispersive Spectroscopy (EDS-NS7-7911) was employed to observe the evolutions of microstructural characteristics of geopolymer-stabilized silty sands after different curing ages, as shown in Fig. 3b. The accelerating voltage range of this device was 5-30 kV. The minimum resolution could be up to 3.0 nm. The structure characteristics of testing samples could be magnified 18-300000 times. When testing, pieces of geopolymer-stabilized silty sands were sprayed with a thin layer of gold and vacuumed to prevent the high-energy electron beam from colliding with air molecules and being absorbed or scattered during the test, and then observed at different magnifications under an accelerating voltage of 15 kV.
Experimental scheme
-
The experimental scheme shown in Fig. 4 could be divided into three parts: the mixing ratio of material components in steel slag-based geopolymer binder, their dosage for silty sand stabilization, and microstructural observations. All prepared specimens in mechanical tests were cured for seven days at the standard conditions suggested by the Standard for Geotechnical Testing Method GB/T 50123-2019 issued by the Ministry of Housing and Urban-Rural Development of China, in which the temperature and humidity of a standard curing environment were 20 ± 3 °C and 90%−95%, respectively. Then these specimens were soaked to saturation. Since these prepared specimens were soaked before loading after standard curing, the saturation process should not have an adverse effect on the early strength of steel slag-based geopolymer binder stabilized silty sands.
(1) Tests on the mixing ratio of material components in steel slag-based geopolymer binder
Soil stabilization practices indicated that the dosage of cement for soil stabilization was generally 8%−15%[4]. Some studies on using metakaolin-based or fly ash-based geopolymers in soil stabilization showed that the amount of binder was close to 15%[5, 6]. Meanwhile, considering that the single-variable method was used for the experimental design of this study, a constant binder consumption should be used for determining the mass mixing ratio of material components in steel slag-based geopolymer binder. Therefore, the total mass ratio of steel slag-based geopolymer binders was assumed to be 15% for investigating the optimum mixing ratio of their material components. The initial balance of slag to alkaline activator was 2:1, according to the authors' previous research results[3, 20]. The ratios of Na2SiO3 to CaO were designed as 1:0.4, 1:0.6, 1:0.7, 1:0.8, and 1:0.9 to find the optimum alkali activation conditions of steel slag-based geopolymerization. The electronic universal testing machine performed unconfined compression tests to determine the optimum ratio of Na2SiO3 to CaO for preparing the alkaline activator. When the relative ratio of Na2SiO3 to CaO in the alkaline activator was selected, the ratio of slag to alkaline activator was readjusted to explore their optimum mixing ratio. The ratios of slag to alkaline activator were designed as 1:0.3, 1:0.4, 1:0.5, 1:0.6, 1:0.7, and 1:0.8. Then the optimum mixing of steel slag-based geopolymer binder could be obtained from a compressive analysis of the above results.
(2) Dosage of geopolymer binder for silty sand stabilization
Based on the above-obtained mixing ratio of geopolymer binder, their powder mixtures were first prepared by dry blending. Then unconfined compression tests on silty sand stabilized with geopolymer binder were re-conducted. The mass mixing ratios of geopolymer binders were designed to vary from 8%, 10%, 12%, 14%, to 16%. The optimum dosage of geopolymer binder for silty sand stabilization thus could be determined when the geopolymer-stabilized silty sand achieved the maximum compressive strength.
(3) Microstructural observation of geopolymer stabilized silty sand
The microstructural characteristics and elemental concentrations of primary components in geopolymer-stabilized silty sand cured for 0, 1, 3, and 7 d were observed by Scanning Electron Microscope (SEM) and Energy Dispersive X-ray Spectroscopy (EDS) at different magnifications. The dosage of geopolymer binder was the obtained optimum mixing ratio. The SEM images zoomed in 500 times were used to analyze the structural compactness of the soil sample through the features of cutting surfaces, the contacts between large particles and small particles, and the pore size and distribution. The SEM images zoomed in 5,000 times were used to observe the characteristics of micro-particles and micro-pores and the formation of gels. The statistical chemical element observation was conducted randomly on the surface of geopolymer-stabilized silty sand samples.
Specimen preparation
-
The silty sands were dried in a 105 °C oven for 24 h and then rolled and sifted through a 2-mm sieve before sampling. Then the dry silty sand samples were mixed with geopolymer binder with a specific water dosage several times. The initial water content of the silty sand samples in this study was invariant. Since this study aimed to apply geopolymer binder in the grouting reinforcement of soft soils, a constant ratio of water to geopolymer was adopted to be 1.0. Considering that the water-binder ratio of grouting slurry suggested in Specification for Mix Proportion Design of Cement Soil JGJ/T 233-2011 issued by the Ministry of Housing and Urban-Rural Development of China was 0.4−1.3 and the most commonly used value in soil stabilization practices was 1.0, the water-binder ratio for specimen preparation was fixed at 1.0. It should be noted that a constant water-binder ratio could lead to the final water consumption in soil stabilization increasing with the dosage of the binder. When sampling, a specimen preparation device's inner surface with a diameter of 39.1 mm and height of 80.0 mm was daubed with Vaseline. Then the wet mixture of silty sand and geopolymer binder was filled into the preparation device and compacted by mechanical vibration. The density of prepared specimens was 1.936−1.947 g/cm3. The water content of silty sand specimens stabilized with 8%, 10%, 12%, 14%, 15%, and 16% of geopolymer binder were 38.3%, 39.7%, 41.17%, 42.4%, and 43.6%, respectively. Their porosities were 4.67%, 4.54%, 4.44%, 4.34%, and 4.26% in turn. All specimens were placed in a curing box with standard conditions for 24 h. Then, they were demolded and cured under the same conditions for another six days. When the curing age was completed, these specimens were soaked to saturation for mechanical tests. For the microstructural observation, the specified geopolymer-stabilized silty sand specimens were cut, dried, polished, and flattened into small pieces of about 10 mm × 10 mm × 3 mm. These small pieces were then sprayed with gold and vacuumed to prevent the absorption or scattering of the high-energy electron beam from hitting the air molecules during testing.
-
Figure 5 shows the unconfined compressive strength variation of geopolymer-stabilized silty sands with different ratios of Na2SiO3 to CaO in the alkaline activator. It can be found that the unconfined compressive strength of geopolymer-stabilized silty sands increased first and then decreased as the relative ratio of Na2SiO3 to CaO decreased. The optimum mechanical performance could be achieved when the ratio of Na2SiO3 to CaO was 1:0.6. The possible reason for this ratio may be that when the ratio of Na2SiO3 to CaO was less than 1:0.6, the CaO content was relatively high. The hydration of relatively excessive CaO would generate excess Ca(OH)2 with the decreasing ratio of Na2SiO3 to CaO, causing local shrinkage and cracking within silty sand samples (just like lime soil and cement soil)[20], thereby affecting the mechanical performance improvement of geopolymer stabilized silty sands. These defects should be significantly responsible for their reduction. When the ratio of Na2SiO3 to CaO was greater than 1:0.6, the CaO content was relatively low[23]. Although the limited alkaline environment could dissolve the active components into SiO44− and AlO45−, it may not be enough to ensure a complete polymerization of active ingredients (SiO2 and Al2O3) in the precursor, thereby resulting in a limited production of geopolymer gels[3,20]. Hence, the strength improvement of silty sand was inefficient. This conclusion was in line with that found in previous studies.
Figure 5.
Variation of unconfined compressive strength of geopolymer stabilized silty sands at different ratios of Na2SiO3 to CaO in the alkaline activator.
Figure 6 illustrates the variation of unconfined compressive strength of geopolymer stabilized silty sands with different ratios of steel slag to alkaline activator. It can be found that the unconfined compressive strength of geopolymer-stabilized silty sands increased first and then slightly decreased as the ratio of slag to alkaline activator decreased. The optimum mechanical performance improvement could be achieved when the ratio of slag to alkaline activator was 1:0.7. That the performance improvement of silty sands was weakening may be that when the ratio of slag to alkaline activator was less than 1:0.7, the precursor for polymerization was relatively insufficient. Although the alkaline environment formed by the hydration of the alkaline activator could result in a complete polymerization of active ingredients (SiO2 and Al2O3) in the precursor, the production of gels was significantly controlled by the amount of the precursor. With the increasing dosage of the precursor, more gels were generated, thus causing a continuous growth in mechanical performance[24]. When the ratio of steel slag to alkaline activator was greater than 1:0.7 (namely, the alkaline activator content was relatively low), the weak alkaline environment might be challenging to promote all active ingredients in the precursor polymerizing. This weak alkaline environment would also result in a slow reaction rate. Both of these reasons caused the mechanical performance improvement not to increase but decrease. According to the results presented in Figs 5 & 6, the final optimum mixing of Slag:Na2SiO3:CaO could be 80:35:21.
Figure 6.
Variation of unconfined compressive strength of geopolymer stabilized silty sands at different ratios of slag to alkaline activator.
Optimum dosage of geopolymer binder for silty sand stabilization
-
Figure 7 presents the unconfined compressive strength of silty sands stabilized with different doses of steel slag-based geopolymer binders. It can be observed that the unconfined compressive strength of silty sand increased first and then decreased with the increasing dosage of geopolymer binder. The maximum compressive strength of geopolymer-stabilized silty sands could be achieved with an average of about 125 kPa when the dosage of steel slag-based geopolymer was 15% in weight. The compressive strength increasing initially and then decreasing could be due to the following: when the dosage of steel slag-based geopolymer was less than 15%, the gel formed by the hydration and polymerization of steel slag-based geopolymer would contribute much more to the strength improvement of silty sands than the strength loss due to the shrinkage and cracking induced by the hydration of CaO. On the contrary, when the dosage of steel slag-based geopolymer was greater than 15%, the more steel slag-based geopolymer used would lead to more CaO being produced in silty sand. It is well known that silty sands generally possess weaker cementation. At the same time, the large amount of Ca(OH)2 formed by the hydration of CaO might result in more significant dry and shrinkage cracking in geopolymer-stabilized silty sands and begin to be the predominant factor of soil strength. Hence, the strength of silty sands decreased with the dosage of steel slag-based geopolymer. Overall, adding the geopolymer binder within a particular level could benefit the mechanical performance improvement of silty sands. The optimum dosage of steel slag-based geopolymer for silty sand stabilization from a perspective of rational utilization of resources and environment-friendly should be 15%.
Figure 7.
Variation of unconfined compressive strength of silty sands stabilized with different dosages of steel slag-based geopolymer binder.
Microstructural evolution of geopolymer stabilized silty sand
-
Figure 8 presents the microstructural characteristics and elemental concentrations of primary components in geopolymer-stabilized silty sands at different curing ages. It can be observed that the structural compactness and particle contact state of geopolymer-stabilized silty sands were improved significantly over the curing age. The SEM images of dry geopolymer stabilized silty sands (cured for 0 d) showed that they had typical granular characteristics in the microstructure. No cementitious contacts among particles were found at the initial stage. The SEM images of geopolymer stabilized silty sands cured for one day illustrated that the primary contact of soil samples at a magnitude of 500 times was particle-aggregate. Still, it didn't exclude cementitious connections since these contacts might be enhanced by CSH gels originally from the reaction of Na2SiO3 and CaO in water discovered from the SEM images at a magnitude of 5,000 times. These images also illustrated that there were loose contacts among particles accompanying large cracks, and a large amount of hexagonal tabular calcium hydroxide could be observed. With the development of the curing age, the size of overhead pores and cracks in geopolymer stabilized silty sand decreased, the amount of large agglomeration became more and more, and the main link among particles became the cementitious contact. When the curing age reached seven days, the previous relatively large pores and cracks disappeared dramatically. The structural compaction of silty sands improved significantly compared with that at the initial stage. The SEM image at a magnitude of 5,000 times demonstrated that the loose granular units of silty sands were wrapped and connected by amorphous gels. The elemental concentrations of primary components in geopolymer-stabilized silty sands at different curing ages indicated that the mass ratio of activated silicon and aluminum components increased over the curing age. In contrast, that of calcium components was the opposite. This significant difference may be that the hydration of CaO promoted the formation of a strong alkali environment and resulted in more and more silicon and aluminum components taking part in the hydration reaction of CSH and CAH and the polymerization of silicon and aluminum minerals.
Figure 8.
Microstructural and chemical composition evolution of geopolymer stabilized silty sands at different curing ages.
Data availability
-
The raw data supporting the conclusions of this article will be made available by the authors without undue reservation.
-
The strength improvement of silty sands was significantly controlled by their material composition and reaction conditions. This study employed the steel slag as the precursor and the mixture of Na2SiO3 and CaO as the alkaline activator for preparing the geopolymer binder. The influence of the mixing ratio of the precursor and alkaline activator and the dosage of steel slag-based geopolymer binder on the strength improvement of silty sand was investigated, and the evolution of the microstructural characteristics of geopolymer stabilized silty sand was observed and discussed to discover the strengthening mechanism. Some main conclusions were obtained:
(1) The mechanical performance of geopolymer-stabilized silty sands was indeed affected by the relative ratio of slag and alkaline activator. Too much or too little ratio of slag, Na2SiO3, and CaO would result in poor strength improvement. The optimum mixing ratio of Slag, Na2SiO3, and CaO for preparing steel slag-based geopolymer was 80:35:21.
(2) The strength of geopolymer stabilized silty sands increased first and then decreased with the dosage of geopolymer binder. The optimum dosage of geopolymer binder for silty sand stabilization was 15% in weight to the dry soil.
(3) The microstructural characteristics of geopolymer-stabilized silty sands demonstrated that silty sands' structural compactness and integrity could be enhanced remarkably over the curing age. The cementitious and agglomeration effects were responsible for the strength improvement of silty sand. This research could provide a reference for geopolymer-stabilized silty sand.
This research was funded by the National Natural Science Foundation of China (41902282), the Science and Technology Planning Project of Jiangsu Province (No. BE2022605), the Science and Technology Development Planning Project of Nanjing, China (Grant No. 202211011), and the Science and Technology Planning Project of Zhejiang Provincial Traffic Department, China (No. 2021038). The authors appreciate all reviewers' constructive and helpful comments.
-
The authors declare that they have no conflict of interest.
- Copyright: © 2022 by the author(s). Published by Maximum Academic Press on behalf of Nanjing Tech University. This article is an open access article distributed under Creative Commons Attribution License (CC BY 4.0), visit https://creativecommons.org/licenses/by/4.0/.
-
About this article
Cite this article
Wang S, Chen Z, Wu Z, Gu L, Su J, et al. 2022. Mechanical properties and strengthening mechanism of silty sands stabilized with steel slag-based geopolymer binder. Emergency Management Science and Technology 2:15 doi: 10.48130/EMST-2022-0015
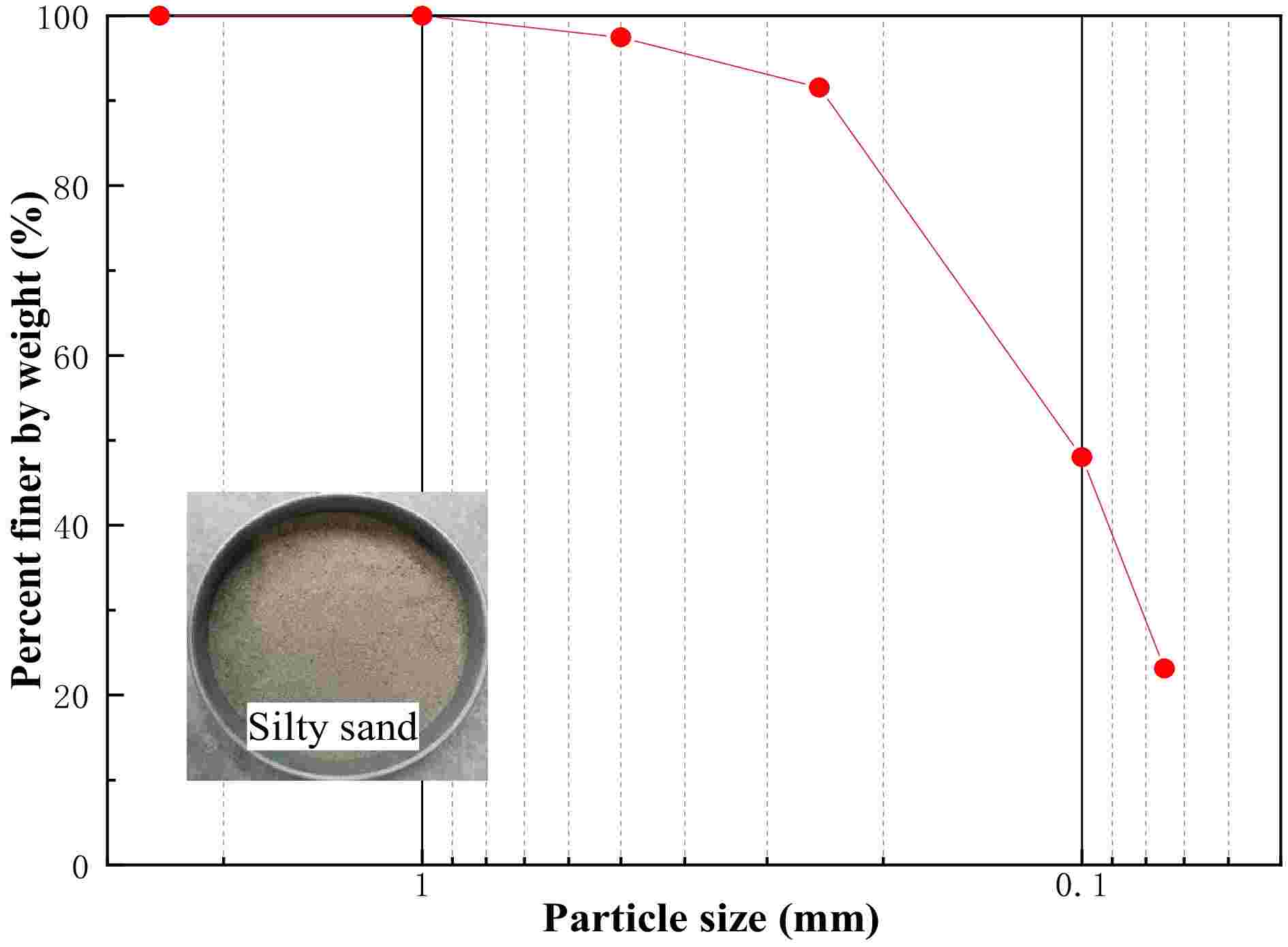