-
Underground structures are generated during the production or construction process of underground spaces, and different underground structures face different underground environments and disaster risks. For example, in the deep underground coal mining process, the support structures of tunnels are established in the coal and rock environment, and face hazards caused by rocks and underground water, such as rock bursts, gas outbursts, and underground water leakage. These problems are inherent in the deep rock mass environment and require a deep understanding of the mechanical behavior of deep rock masses and the laws of underground water in order to better serve safety production through monitoring means.
For urban underground space development, due to the shallow depth, underground structures exist in the soil environment, and thus the interaction between the soil and structures becomes the main contradiction. The static and dynamic mechanical behavior of soil and the interaction between soil and underground structures are the key points that need to be mastered. With the acceleration of urbanization, underground structure engineering has become an important component of urban construction. However, the construction of underground structure engineering is difficult, and there are safety risks due to the complex construction environment. In order to ensure the safety of underground structure construction, monitoring and risk warning assessments are needed. This article will explore the monitoring of underground structure construction, risk assessment methods, and their applications.
The response to external load of underground structure and above-ground structure is very different due to different environments. For example, under the action of earthquake load, the seismic force on the above-ground structure is often manifested as the failure mechanism dominated by inertial force, while the underground structure is due to the interaction between the structure and the surrounding rock mass or soil mass under earthquake action. Therefore, the failure result of underground structures is usually caused by the extrusion or deformation of rock mass or soil mass to the structure. Through statistical analysis of the dynamic failure results of underground structures under different buried depths, the investigation results show that the damage of underground structures built in soil is usually more serious than that in hard rock mass, and the damage degree of underground structures decreases with the increase of the thickness of the cover layer. The underground structure based on the development of urban underground space is usually located in the shallow soil stratum space, and the prevention and early warning of earthquake disasters are still mainly based on above-ground monitoring. Meanwhile, the underground structure has a passive defense design for earthquake action. On the other hand, the surrounding medium of underground structures such as coal mines or hydropower stations in deep rock mass is rock mass, and the occurrence environment of rock mass is more complex, with prominent problems such as high ground stress, high ground temperature and high osmotic pressure, presenting strong sudden water gushes, high-strength rock burst, sustained large deformation of soft rock, boulder collapse, coal mine rock burst and other phenomena. Therefore, the main disasters faced by deep underground engineering structures are not earthquake disasters, but the external environment determined by the stress state of rock mass caused by high ground stress. Therefore, it is necessary to set up monitoring schemes for disaster types respectively. For example, for underground structures under shallow soil, such as subway stations, underground shopping malls, underground tunnels and other engineering structures, grating fiber sensors need to be arranged to monitor structural deformation and surrounding soil displacement data. For the deformation monitoring of deep rock mass structure, it is necessary to combine the occurrence characteristics of rock mass and the characteristics of potential damage caused by the outside world to rock mass formation to carry out targeted measurement point arrangements[1−7].
-
Underground space structure in a city is used to expand the urban living space and utilize space. Main underground structures include subway stations, section tunnels, underground shopping malls, underground parking lots, underground integrated pipe corridors among others. Disaster risk sources of underground structures are mainly divided into disasters during construction and disasters during service. In the construction process, changes in the stress field and seepage field of underground rock and soil mass caused by construction activities have damage effects on the existing environment and structure. The damage during service refers to the damage of underground engineering structures formed by normal use or the damage of underground structures caused by earthquakes during normal use. In order to grasp the working state of the engineering structure in the construction stage or the service stage in real time, it is necessary to monitor its condition in order to evaluate the health state of the engineering structure. As the construction process is an orderly loading process with time, the stress of the underground soil layer is in the stage of gradual release, while the corresponding load is gradually applied to the underground engineering structure. The corresponding monitoring objects and monitoring indicators should be able to reflect the characteristics of the above gradual change, such as the horizontal displacement of the supporting structure, the internal force of the supporting pile, and the vertical and horizontal displacement of the surrounding structure.
There are several main measurement methods for construction process monitoring, including the following: Construction monitoring methods for underground structural engineering include surface measurement, underground measurement, and sensor monitoring. Surface measurement refers to measuring the deformation of excavation using traditional measurement methods, such as total station and level. Underground measurement refers to monitoring the support structure and underground building using underground measuring instruments, such as inclinometers and pressure gauges. Sensor monitoring refers to fixing sensors at positions such as excavation, support structures, and underground buildings to collect data for monitoring. Types of sensors include displacement sensors, pressure sensors, and seepage meters. In the monitoring of underground engineering structures, fiber optic grating sensors are used to measure the stress and strain of underground structures. In 1991, Nanni et al.[8] embedded fiber optic grating sensors in concrete structures for the first stress-strain test of structures. In 1998, Ansari & Yuan[9] analyzed the strain transmission theory of fiber optic sensors in more detail, assuming that the strain at the center of the embedded fiber optic grating is the same as that of the substrate, and obtained the axial strain distribution of the fiber optic grating. In addition, other researchers[10−14] further studied the accuracy of fiber optic grating sensors in concrete measurement.
-
Monitoring and measurement technology for underground structures usually focuses on the stress and displacement of the support structure of excavation earthwork, and the information sources and monitoring schemes are relatively simple. For the deformation monitoring of engineering structures in soil layers, it is generally based on the deformation of the soil during excavation and the changes in soil pressure, and the deformation and stress mechanisms in shallow strata can be well predicted, so monitoring points can be arranged accordingly. However, for tunnels with depths of hundreds or even thousands of meters, such as those in coal mining, the underground deep rock mass is structurally complex and subject to complex structural stresses. The rock mass itself has various types of cracks, joints, and heterogeneity. In addition, it is always in a dynamic process of construction and production, which can cause dynamic stress problems such as rockburst, gas outburst, and underground tunnel water inrush[15−18]. Therefore, for the monitoring of deep rock masses, although increasing the monitoring density can improve the monitoring effect, the workload and equipment costs will increase exponentially. In addition, there are differences between the monitoring devices and monitoring systems, and the information is difficult to share. Moreover, the generation mechanism and rules of impact dynamic behavior of deep rock masses are not yet clear, and the dynamic change rules have not been fully grasped.
Currently, there are still some difficulties in the dynamic monitoring of deep rock masses, including: (1) the effective monitoring range of deep rock masses is difficult to determine; (2) it is difficult to accurately classify the monitoring warning levels; (3) the monitoring sensors of deep rock masses are difficult to deploy; and (4) there is a time lag in knowing the existence of on-site production based on monitoring warning information. For the problem of fault water inrush in deep rock masses, the monitoring warning time domain is first determined to be the stage of crack initiation, and then the spatial distribution range of monitoring warning space domain is determined using the key water-blocking layer theory[19] and geophysical methods. Whether the fault zone produces water inrush phenomenon needs to analyze the temperature field of sandstone strata rich in groundwater and the change of seepage pressure field to determine the monitoring warning threshold. Then, sensors are used to implement control in the determined monitoring space domain, and the extension trend of deep rock mass fracture zone is sent in a timely manner. According to the deep rock mass monitoring warning discrimination criteria, the warning levels during the mining process are classified, which can achieve safe mining of coal resources. Generally, the formation mechanism of impact ground pressure in deep rock masses can be roughly divided into the following three types: (1) Deep strain type impact ground pressure, which accumulates a large amount of elastic energy in the surrounding rock under high stress in deep rock masses. Once the unloading confinement pressure is released, the elastic energy is rapidly released, causing impact disasters. (2) Deep hard roof type impact ground pressure. The exposed area of the deep hard roof in the goaf is much larger than in the shallow part, and more energy is accumulated. When it suddenly fractures, a large amount of energy is input into the coal rock system, causing rapid damage to the coal and causing impact disasters. The difference in the combination of the hard roof with the coal seam under deep conditions has a more prominent impact on the degree of impact. (3) Deep fault slip type impact ground pressure. When a fault is activated, a large amount of elastic energy accumulates in the top plate near the fault under high overlapping stress and is suddenly released, which accelerates the sliding of the fault and causes rapid damage to the coal seam, resulting in an impact disaster. As shown in Figs 1 and 2, the comparison view of impact ground pressure failure can be displayed.
There are various methods for early warning and monitoring of impact ground pressure disasters[20−26]. As shown in Fig. 3, they can be broadly classified into two categories: physical methods and mechanical methods. Physical methods utilize various instruments to capture information about energy changes released to the outside world during rock mass rupture, such as waves, sound, and electrical resistivity information. The potential development state of impact ground pressure is obtained by interpreting the above information. Mechanical methods rely on equipment to directly test the rock mass. For example, the drilling debris method is simple, practical, and intuitive, but the number of boreholes is small, the detection range is limited, and important blind spots are often missed in practical operation. Although the deformation-based dynamic top plate instrument method and roadway surface displacement method are simple and practical, their disadvantages are limited deployment range and small monitoring range. The borehole stress meter method also suffers from the problem of limited monitoring range.
Another method for testing impact ground pressure is to use displacement meters installed in the blank area between roadway support anchor rods. Multiple displacement meters are arranged on the cross section to monitor the deformation at various locations. For deep rock mass water inrush issues, fiber optic grating demodulators, fiber optic grating thermometers, fiber optic grating seepage pressure gauges, collection hosts, and signal transmission fiber optic cables can be used. They are installed on the roadway cross section, and the sensors are installed in the boreholes of the deep rock mass to collect water temperature and pressure signals for monitoring the direction of water flow[27−33]. Whether there is a sudden water inflow during the initiation stage of fault fissures depends on whether the fissures can cause the overlying aquifers to move along the fault zone and be uplifted along the fractures in the coal seam roof. By analyzing the changes in the mixed water temperature field and seepage pressure field in the monitoring area, the monitoring and warning threshold can be determined, and a warning sign for delayed water inrush monitoring of faults can be established.
Blast vibration monitoring technology is a technique that monitors blast vibration using vibration sensors. This technology is usually used in mining, construction sites, tunnels, and other situations that require blasting operations to ensure that the impact of blasting operations on the surrounding environment is within acceptable limits. Vibration sensors are devices that measure the vibration of an object, usually using accelerometers or vibration sensors to measure the acceleration or velocity of the object. When an object vibrates, the vibration sensor captures the vibration signal by measuring the acceleration or velocity. In blast vibration monitoring, vibration sensors are installed in the area to be monitored, such as surrounding buildings or the ground. During the blasting process, the vibration sensor captures the vibration signal caused by the blast and transmits the signal to the data acquisition system or monitoring system for processing and analysis. By analyzing the vibration signal, the impact of the blasting operation on the surrounding environment, such as the structural safety of buildings, foundation stability, and environmental noise, can be evaluated. If the vibration signal exceeds the preset safety threshold, the monitoring system will issue an alert and take necessary measures to protect the surrounding environment and personnel safety.
Microseismic monitoring technology is mainly used to record the vibration energy during mining operations, and then analyze and determine the direction of the vibration. By locating the epicenter, the overall dynamic behavior of the mine can be evaluated. Microseismic monitoring activities are carried out around the entire mining area, comprehensively recording the situation of microseismic activity, achieving accurate calculation of the source location and micro-positive energy, and providing powerful data information for the assessment of rockburst hazards. The ground sound monitoring technology used mainly involves configuring low-frequency sensors to achieve comprehensive monitoring of the mining-induced impact zone.
As shown in Fig. 4, a monitoring procedure can be exhibited. Generally, centralized monitoring of the production area is carried out using corresponding data information, such as comprehensive analysis of frequency and energy, to determine the main rules of ground sound activity, and then infer the stress and damage degree of the coal and rock mass, analyze the stability of the coal and rock mass, and accurately judge the impact risk. In addition, electromagnetic radiation methods can also be used. Typically, when the coal and rock mass fractures or breaks under load, electromagnetic radiation and sound emission signals are produced. By analyzing the dynamic changes of various signals, accurate early warning of coal and rock dynamic disasters can be achieved, providing support for safety supervision. Actual monitoring projects usually use a comprehensive approach using multiple methods. First, the occurrence mechanism of rockburst is preliminarily judged based on the principles of rockburst, and severe coal and rock mass damage and high stress concentration are usually the precursor of rockburst. By in-depth exploration of microseismic, electromagnetic radiation, and drilling debris methods, the approximate occurrence range of rockburst can be determined. Microseismic monitoring is used for real-time monitoring of the entire system, and drilling debris methods are used to monitor key local areas, thereby constructing a multi-level monitoring system.
To effectively prevent landslide damage in open-pit mining, the team led by He et al.[34] Manchao from China University of Mining and Technology invented the Negative Poisson's Ratio (NPR) anchor and applied it in open-pit mining engineering. NPR technology has also been applied in the engineering monitoring of large slopes[24, 26, 35]. Based on the mechanism of landslides, a dual-block catastrophic mechanical model was proposed, and the sudden decrease in sliding Newton force between the landslide body and the sliding bed was used as a criterion for monitoring landslide initiation. Based on this principle, the 'Landslide Newton Force Remote Monitoring and Early Warning System' was developed, which can effectively monitor the development process of landslides in real-time. According to the curve of the landslide development process, it is divided into four stages, and a four-stage early warning mechanism is established. Through this warning mechanism, the status of the slope can be accurately judged, providing accurate and real-time warning information and reference for mining schemes in open-pit mining.
-
In the current urban development process, due to various factors affecting ground transportation and limited usage area, underground engineering has become a direction for infrastructure growth dedicated to tapping the potential of the city. However, underground engineering is different from above-ground engineering and is greatly influenced by the surrounding environment, especially the mechanical properties of the geological layers. Therefore, for underground structural engineering construction such as foundation pits, underground shopping malls, subway stations, underground tunnels, etc., there are inevitably significant safety issues. This requires planned and targeted construction process monitoring, which spans the entire construction process, and requires real-time feedback of monitoring data to understand the ground settlement, underground structure displacement, and changes in groundwater level in detail. Mastering the change laws is helpful for judging the safety of underground structures[36−46].
In addition to the commonly used method of regularly monitoring underground support structures or underground structures by deploying sensors, there are currently some new monitoring technologies being adopted. For example, Ji et al.[47] used distributed fiber optic measurement to measure the axial force and strain of prestressed anchor rods. The strain monitoring fiber optic was tightly wrapped with 5 mm steel strands and temperature compensation fiber optic was used to eliminate the temperature effect on fiber optic monitoring. The distributed strain monitoring fiber optic was fed into the anchor rod hole along the rod body, and after grouting, the distributed fiber optic and the grouting formed a whole and deformed together, with the strain of the distributed fiber optic being the same as that of the anchor rod body. The installation diagram of distributed optical fiber in anchor rod is shown in Fig. 5.
Figure 6 shows the arrangement of strain fibers and temperature compensation fibers on the steel strands, with each steel strand corresponding to a strain fiber sensor. The monitoring results demonstrate that monitoring strain can reflect the bond force between the anchoring body and the soil, providing guidance for the design parameters of the anchor rod, and has a considerable degree of engineering application value.
The monitoring of horizontal displacement, especially for underground engineering support structures, has always been a focus. Currently, automated monitoring of deep-level horizontal displacement in deep foundation pits mainly uses fixed inclinometers, with sensor vertical spacing generally between 1−3 m. With the promotion of MEMS technology, flexible inclinometers have gradually been promoted from slope monitoring to enclosure structure monitoring in deep foundation pits, measuring the two-dimensional or three-dimensional deformation of the measurement object. The system has no preferred axis, and adjacent measurement segments can be freely curved, and can be installed vertically and horizontally. When installed vertically, the horizontal displacement of the measurement object at different depths can be obtained, while horizontal installation obtains the corresponding vertical displacement.
Figure 7 shows the physical diagram of the strain annular array displacement sensor (SAA) sensor, which is composed of multiple sub-segments connected by flexible joints. Each sub-segment consists of MEMS sensors and has a length of 0.3−0.5 m, and is externally equipped with wear-resistant and corrosion-resistant materials. The total length can be customized according to the test object, and each sub-array can bend up to a maximum angle of 60 degrees. The displacement sensor consists of 64 sub-arrays and has a total length of approximately 32 m, with an end-point displacement measurement accuracy of 1.5 mm. The above sensors can be effectively used for landslide displacement monitoring and the horizontal displacement of support piles in foundation pit engineering.
Discussion on monitoring standards for underground foundation pit engineering, a comprehensive and rigorous monitoring system, is usually established during the construction process, including monitoring of the surrounding environment[48−62]. Specific monitoring content includes lateral deformation of support structures, axial force of concrete supports, and monitoring of columns and ground settlement. By obtaining real-time monitoring data of the foundation pit and analyzing the development trend of the data, construction and the safety of the foundation pit can be ensured, and the impact on the surrounding environment can be minimized to the greatest extent possible. For common foundation pit engineering projects, the control values of monitoring data are shown in Table 1.
Table 1. Monitoring items and limits for excavation engineering.
Monitor items Maximum
valueRate
warning
(mm/d)Control
valueWall displacement (mm) Supporting pile 1 3 35 Supporting axial force (kN) Supporting axial force 1 13,777 Water table (mm) Water table 1 2,000 Column settlement (mm) Column 1 2 20 Ground displacement (mm) Ground 1 3 35 Horizontal displacement of supporting pile (mm) Pile 3 20 Vertical displacement of supporting pile (mm) Pile 3 20 As shown in Table 1, during the excavation phase of foundation pit engineering, the horizontal displacement of the supporting pile injection will increase, and the maximum surface settlement value will increase. Additionally, the supporting axial force will increase rapidly. The allowable limit values corresponding to each monitoring item indicate the maximum allowable deformation data of the supporting structure and the bearing capacity of the concrete support. By continuously monitoring the measuring points on the foundation pit or retaining structure, the daily settlement deformation rate and cumulative value can be obtained. By utilizing monitoring data, the advantages of informationized construction can be reflected, i.e., using monitoring data to provide feedback for guiding construction plans. For the waist beam position where deformation needs to be strictly controlled, controlling the horizontal displacement of the supporting pile can be achieved by applying prestress to ensure the safety and stability of foundation pit engineering.
For monitoring the soil pressure on the outside or inside of the foundation pit, a soil pressure box can be used for testing. The embedded test method is commonly used when conducting soil pressure monitoring. In the process of using the embedded monitoring method, the embedding operation and monitoring requirements need to be matched to ensure that the pressure film is in a vertical state, the force surface is in close contact with the detected object, and protection work is done for the pressure film. Accurate records of relevant monitoring data should be made. After the soil pressure monitoring is completed, the pressure film should be carefully inspected to ensure that there are no problems with damage, in order to avoid distortion of the recorded data. In fact, due to the contact problem between the soil and the structure, the pressure that the soil pressure film bears is not always loaded vertically. Usually, it bears a certain amount of friction, which can lead to inaccuracies in the measured soil pressure values.
-
The tunnel surrounding rock deformation monitoring technology is a technology that uses strain gauges, measuring instruments and other equipment to monitor the real-time strain changes of the surrounding rock in a tunnel, in order to warn of the deformation risk caused by instability or cracking of the rock. This technology is mainly used to ensure the safety and reliability of tunnel construction and operation. The strain gauge is an instrument used to measure the strain changes of an object. By installing the strain gauge on the surface of the surrounding rock, the strain gauge can record the strain value when the rock deforms, and transmit this data to a computer for processing through a sensor. The measuring instruments include level gauges, inclinometers, total stations, etc. By measuring the tilt and horizontal degree of the surrounding rock, the deformation of the tunnel surrounding rock can be accurately monitored. Through tunnel surrounding rock deformation monitoring technology, the deformation of the tunnel surrounding rock can be monitored in real time, and signs of rock instability or cracking can be discovered in a timely manner, and corresponding measures can be taken to reduce risks during tunnel construction and operation. In addition, tunnel surrounding rock deformation monitoring technology can also provide valuable data support for tunnel maintenance and management, helping tunnel managers to timely understand the safety status of the tunnel, carry out maintenance and repairs, and prolong the service life of the tunnel, ensuring the safety and reliability of tunnel operation.
The main steps of tunnel surrounding rock deformation monitoring technology include geological exploration, surrounding rock mechanical property testing, monitoring equipment installation, data collection and analysis, etc. Common monitoring equipment includes strain gauges, displacement sensors, pressure sensors, etc. By collecting data such as surrounding rock deformation, stress and pressure through these devices, analysis and evaluation can be conducted to determine the stability and safety of the tunnel surrounding rock.
Tunnel surrounding rock deformation monitoring technology has been widely used in various tunnel engineering projects such as highway tunnels, railway tunnels, water conservancy tunnels, and subway tunnels. Timely discovery and treatment of surrounding rock deformation problems during tunnel construction and operation are of great significance for ensuring the safe operation of tunnels and prolonging their service life.
-
The monitoring frequency of underground structure engineering construction should be determined based on specific circumstances. Generally, the monitoring frequency in the early stage of construction should be higher than that in the later stage. During the initial stage of excavation, monitoring should be conducted daily to promptly grasp the stability and deformation of the earthwork. The monitoring frequency in the later stage of construction can gradually decrease, but the monitoring data should cover the entire construction process. Therefore, construction safety monitoring and risk assessment of underground structure engineering are particularly important.
Construction safety monitoring of underground structure engineering refers to real-time monitoring of the construction process through monitoring technology during the construction process of underground structure engineering to promptly identify and solve safety hazards and ensure construction safety. The monitoring of underground structure engineering construction mainly includes monitoring of soil displacement, changes in groundwater level, and structural deformation. Among them, soil displacement monitoring is the focus of underground structure engineering monitoring. During the construction process of underground structure engineering, soil displacement is influenced by various factors such as groundwater level, soil compaction, underground pipelines, etc. Therefore, continuous monitoring and analysis of soil displacement are needed to promptly identify and solve problems where the soil displacement is too large.
Safety accidents can occur at any time during the construction process of underground structure engineering, so it is necessary to conduct risk assessment and warning evaluation of the construction process. The risks in the construction process of underground structure engineering mainly include soil stability, groundwater level, and underground pipelines. By predicting and evaluating the risks that may occur during the construction process, corresponding measures can be taken in advance to prevent accidents.
In the safety monitoring and risk assessment of underground structural engineering construction, the selection and use of monitoring technology are particularly important. By reviewing the latest underground engineering construction monitoring technology, the following conclusions can be drawn:
(1) Analyzing the disaster-causing mechanism in the underground engineering construction process, and using laboratory experimental techniques to reproduce the underground disaster process at the production site is conducive to engineering technicians' in-depth understanding of the entire process of underground disaster incubation. Based on the disaster-causing principle in the production process, new ideas can be proposed to prevent and mitigate disasters, such as using high deformation resistance anchor rods to effectively predict the sudden drop phenomenon of Newton's force formed by landslide bodies, which can provide early warning and guide the production progress of open-pit mines, and ensure maximum production efficiency while achieving the goal of controlling landslide disasters safely.
(2) For certain underground engineering projects, personalized warning signals should be proposed in conjunction with regional geological characteristics, such as combining local construction standards and local underground engineering monitoring technical specifications to determine specific indicator limits. For example, in the sand and gravel formation, the horizontal displacement limit of the support pile can be controlled at 20 mm, and this limit is based on the consideration that the sand and gravel formation has relatively high stiffness and strength characteristics. If the above limit is applied to underground engineering in areas with thicker silty soil, it is not applicable. On the one hand, the pile-anchor support system used in hard soil areas is not suitable for silty soil layers. On the other hand, it may cause unnecessary increases in engineering costs, making it economically unfeasible. Therefore, the monitoring limit values for underground engineering in silty soil areas should be based on local monitoring technical specifications as guidance indicators.
(3) Based on the significant differences between deep and shallow strata in underground engineering, the surrounding medium of the former is rock, while the latter is mostly soil material. Therefore, the physical properties of rock and soil are very different, which causes significant differences between deep and shallow underground engineering. Both should be executed in accordance with relevant specifications.
-
The authors confirm contribution to the paper as follows: study conception and design: Wan Z; draft manuscript preparation: Wan Z; data curation: Qin J; investigation and data analysis: Wei Z. All authors reviewed the results and approved the final version of the manuscript.
-
The data are available from the corresponding author on reasonable request.
-
The authors declare that they have no conflict of interest.
- Copyright: © 2023 by the author(s). Published by Maximum Academic Press on behalf of Nanjing Tech University. This article is an open access article distributed under Creative Commons Attribution License (CC BY 4.0), visit https://creativecommons.org/licenses/by/4.0/.
-
About this article
Cite this article
Wan Z, Qin J, Wei Z. 2023. Overview of technical research on safety monitoring, early warning, and risk assessment for underground structural engineering construction. Emergency Management Science and Technology 3:18 doi: 10.48130/EMST-2023-0018
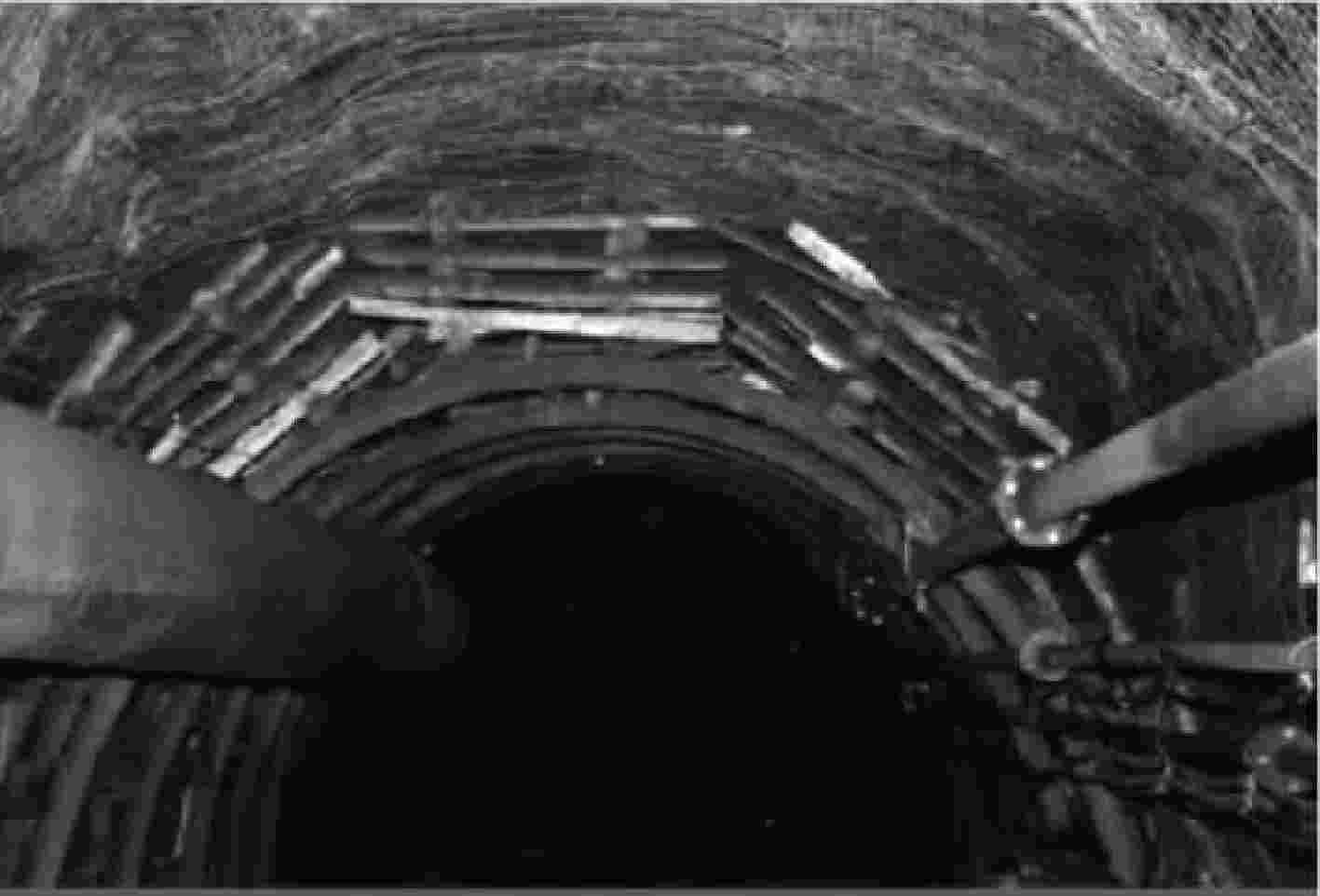