-
Wireless power transfer, especially via resonant inductive power transfer (RIPT), is becoming increasingly popular for charging various devices such as Electric Vehicles (EVs), Unmanned Aerial Vehicles (UAVs), and consumer electronics such as cellphones[1,2]. This technology offers users a safe and efficient charging experience. With the charging process automated and free from constant user intervention, wireless charging addresses the range anxiety problem in electric vehicles and extends the flight time of UAVs[3,4]. For consumers, eliminating charging cables means no more hassle and clutter, keeping their charging areas clean and organized. Figure 1 shows the block diagram of a typical RIPT-based wireless charger.
In Fig. 1, power is transferred from the transmitter to the receiver through resonant inductive coupling. It consists of two inductors that are magnetically coupled through the principle of electromagnetic induction. The air gap between the transmitter and receiver inductors is significantly larger than a conventional transformer. To improve the system's efficiency, both inductors are made to resonate with a bank of capacitors in the transmitter and receiver circuits. These capacitors can be connected to the inductors in a series, parallel, or a combination of series-parallel configuration, resulting in multiple resonant topologies.
For charging applications, load on the RIPT system is some kind of energy storage device. Due to their high energy density and power density, Li-ion batteries are a popular choice for energy storage devices in electric vehicles, UAVs, and consumer electronics[5−8]. Li-Ion batteries are charged using a Constant Current Constant Voltage (CC-CV) method which is shown in Fig. 2.
In Fig. 2, V represents the battery's rated voltage, I denotes the battery current and R indicates the equivalent resistance variation during the CC-CV charging operation of a lithium-ion (Li-Ion) battery. The battery is initially charged with a constant current until its terminal voltage reaches the rated voltage. Subsequently, the charger transitions to a constant voltage output, maintaining the terminal voltage until the battery achieves full charge. This charging technique, known as CC-CV (constant current-constant voltage), leads to an exponential rise in the terminal resistance observed by the charger, depicted by the red curve in Fig. 2. Consequently, the RIPT (Resonant Inductive Power Transfer) system must be controlled to operate in CC-CV mode.
This paper presents a review of control methods applicable to RIPT systems for charging batteries using the CC-CV mode. Referring to Fig. 1, RIPT systems can be implemented in various configurations depending on the choice of the power converter and compensation topology, it is impractical to address control strategies for every circuit configuration. Therefore, this paper focuses solely on the control method for the Series-Series RIPT (SS-RIPT) system. For the DC-AC converter, H-Bridge topology and for AC-DC converter a Full-Bridge rectifier will be considered. The main contribution is identifying the control variables and utilizing them to achieve the CC-CV mode of operation.
The control strategies for Resonant Inductive Power Transfer (RIPT) systems present a significant concern, and existing literature has yet to address all control strategies comprehensively in a single paper. There is a need for a thorough discussion of these strategies, including their advantages, limitations, and implementation examples, within a single paper. Addressing this gap is essential for advancing future research in this area, which underscores the importance of this review.
-
Figure 3 shows the SS-RIPT-based wireless charger[9−11]. In Fig. 3, only the DC to DC stage has been considered, and the front-end converter (EMI + PFC) stage has been neglected. In Fig. 3, the symbols VP and IP denote the primary side voltage and current, while VS and IS represent the secondary side voltage and current, respectively. LP and LS refer to the primary and secondary side inductances, and CP and CS indicate the primary and secondary side capacitances.
Since the transmitter and receiver sides are mutually coupled through electromagnetic field, therefore battery voltage (VBatt) and battery current (IBatt) can be controlled directly by sensing the VBatt and IBatt or it can be controlled indirectly by sensing the current and voltage of the resonant tank such as IP, VP, IS, and Vs. Figure 4 shows the electrical equivalent circuit of the SS-RIPT link.
In Fig. 4, RL is the equivalent resistance of the battery seen by the secondary side, given by Eqn (1).
(1) The fundamental components of VS and IS are related to VBatt and Ibatt respectively using Eqns (2) and (3).
(2) (3) Referring to Fig. 4, at resonance,
(4) (5) By utilizing Eqns (1)−(5), the relationship between battery voltage and current can be established with primary side voltage and current, as demonstrated in Eqns (6) and (7).
(6) (7) Relationships in Eqn (2), (3), (6) and (7) can be utilized to control the battery voltage and current from the resonant tank variables.
It should be noted that battery current/voltage can also be controlled indirectly by sensing DC link voltage VDC and DC link current IDC. However, for this article, the sole focus was on direct control by sensing VBatt and IBatt and indirect control by sensing resonant tank variables. Figure 5 shows the overall block diagram of the CC-CV controller.
In Fig. 5, a voltage/current controller enables the comparison between the measured output voltage/current and the desired values. The outputs of the controller determine the duty cycle for the PWM (Pulse Width Modulation) modulator. This duty cycle is then compared with a ramp signal to generate PWM pulses for the inverter or rectifier, which charges the battery. The PWM block generates a quasi-square wave at the output of the converter as shown in Fig. 6.
As shown in Fig. 6, output voltage and thus current can be regulated by four control variables α+, α-, and β, and the switching period (Ts). Three types of PWM are possible namely: Symmetric Voltage Cancellation (SVC) also known as Phase shift (PWM), Asymmetrical Voltage Cancellation (AVC), and Asymmetrical Duty Cycle (ADC). Detailed descriptions of these PWM techniques have been previously reported[12,13]. In Fig. 5, a selection logic is incorporated to switch between Constant Current (CC) and Constant Voltage (CV) modes based on the battery's state of charge.
Control strategies in resonant inductive power transfer (RIPT) systems are primarily classified into three types, depending on which side's converter is being controlled: primary side control, secondary side control, and dual side control. Primary side control involves regulating the converter of the transmitter (i.e., the DC-AC converter), while secondary side control focuses on managing the converter of the receiver side (i.e., the AC-DC converter). Dual side control, on the other hand, entails controlling both the transmitter and receiver converters simultaneously.
Based on the choice of control signal (reference signals), Table 1 categorizes the control method for SS-RIPT chargers. In Table 1, direct refers to sensing the battery voltage and current directly for feedback and indirect control refers to sensing signal other than load (battery) voltage and current.
Table 1. Classification of control method for SS-RIPT systems.
Type of control Control variables Direct control Primary side, direct control VBatt, IBatt Secondary side, direct control VBatt, IBatt Indirect control Primary side, indirect control (VP, IP) or (VS, IS) Secondary side, indirect control (VP, IP) or (VS, IS) Existing primary side direct control strategies typically rely on wireless communication modules, such as Wi-Fi and ZigBee. In these strategies, charging information is wirelessly transmitted from the secondary side to the primary side and is then used as reference signals for the controller. Although this is a well-established technical solution, many studies have thoroughly analyzed the primary side direct control methods[14−17], and certain challenges persist. These challenges include the additional cost of hardware and software for wireless communication modules, potential communication instability due to strong magnetic field interference, and the unsuitability of wireless communication for specific applications such as underwater or aerospace environments.
To address these issues, some studies have introduced primary side indirect control methods. In Madawala et al.[18], the output power is regulated through the power-frequency droop characteristic of the wireless charging system, eliminating the need for a dedicated communication link. In Chow et al.[19], transmitter-side electrical information is used to regulate the power consumption on the receiver side. However, these methods focus solely on adjusting the output power without addressing the control of charging current and voltage. In Madawala & Thrimawithana[20], a phase-shifted full-bridge inverter is used to achieve constant voltage (CV) charging for the RIPT system, based on the estimated charging voltage from the primary side. However, no further analysis of constant current (CC) charging is provided. In Song et al.[21], while the primary side controller is capable of CC/CV charging for the SS/SP compensated RIPT system, it requires the estimation of load resistance and mutual inductance to control the charging current and voltage. This, in turn, necessitates additional hardware for load resistance estimation and mutual inductance identification, increasing system complexity and overall cost. In Li et al.[22], a primary side indirect control method is proposed to achieve CC/CV charging for the SS compensated RIPT system without the need for load identification, mutual inductance estimation, or dual-side communication.
This review discusses both direct and indirect control strategies. For the indirect control strategy, rather than employing the complex approaches mentioned in the references, a more simplified method is adopted. This method involves deriving equations that establish the relationship between battery current and voltage with the primary and secondary tank currents and voltages, enabling effective control of the battery voltage and current.
The authors acknowledge that dual-side control is also widely used, especially in bidirectional power transfer applications[23−25]. However bidirectional control is not the focus of the current paper and will be covered separately in a different study.
-
In direct control, the battery is charged by directly sensing the battery voltage and current, utilizing them as feedback signals for the controller. Depending on whether PWM is controlling the primary-side converter or the secondary-side converter, direct control can be classified into two categories: Primary-side direct control and secondary-side direct control. Both types are elaborated on in the subsequent subsection.
Primary side direct control
-
This is a very straightforward and easy-to-implement control technique. Figure 7 shows the block diagram of the primary side direct control of the SS-RIPT charger. VBatt and IBatt are used as the feedback signal for the CC-CV controller shown in Fig. 4. PWM signals generated from the CC-CV controller are used to adjust the primary side inverter output to control the voltage and current applied to the battery[15,26,27−29]. The secondary side converter could be a simple uncontrolled rectifier or should be switched to 50% duty cycle in the case of an active rectifier.
By utilizing Eqns (6) and (7), VBatt and IBatt can be manipulated by controlling IP and VP, respectively. To achieve this, a voltage control loop will generate PWM to regulate the output voltage of the inverter, ensuring that IP remains constant, thus operating the charger in CV mode. Similarly, for CC mode, a current control loop will generate PWM to maintain a constant VP, thereby supplying the battery with a constant IBatt.
Secondary side direct control
-
Figure 8 shows the block diagram of the secondary side direct control scheme of the SS-RIPT system.
In Fig. 8, the primary side converter operates at a fixed 50% duty cycle to achieve a square waveform. The secondary side converter functions as an active rectifier[30−34]. For this control method to operate effectively, the secondary resonant tank must be slightly inductive[12]. PWM regulates the IBatt and VBatt through Eqns (2) and (3).
-
In indirect control, battery voltage and current are not used as feedback signals. Instead, primary, or secondary side resonant network variables are used as feedback signals of the CC-CV controller. Depending on whether PWM is controlling the primary-side converter or the secondary-side converter, direct control can be classified into two categories: Primary-side indirect control and secondary-side indirect control. Both types are elaborated on in the subsequent subsection.
Primary side indirect control
-
Figure 9 shows the block diagram of the primary side indirect control scheme of the SS-RIPT system.
In Fig. 9, the average, RMS, or peak value of VP and IP are detected and used as feedback signals for the CC-CV controller. Figure 10 shows the block diagram representation of the average voltage control of the CC-CV controller[35,36]. Similarly, a current controller can be implemented. Equations (6) and (7) are applicable in this control.
Secondary side indirect control
-
Figure 11 shows the block diagram of the secondary side indirect control scheme of the SS-RIPT system.
In Fig. 11, the primary side converter is operated at 50% duty cycle to obtain square wave output. The secondary side converter is operated as an active rectifier. Here the average, RMS, or peak values of VS and IS are detected and used as feedback signals for the CC-CV controller.
-
Existing literature indicates that both direct and indirect control strategies have distinct advantages and limitations. This section provides a comparison of these methods, focusing on their respective advantages and limitations.
Table 2. Comparison between direct and indirect control.
Control strategy Advantages Limitations Primary side
direct controlIt is a straightforward and easy-to-implement control method. The direct use of battery current and voltage as feedback signals for the CC-CV controller simplifies the process of sensing DC variables. This approach reduces the weight and complexity on the receiver side. • The dependence on wireless communication modules for information transmission incurs additional expenses associated with both hardware and software requirements
• The transmitted information is vulnerable to errors, delays, and potential loss.
• Strong magnetic field interference may cause instability in the communication process.Primary side indirect control • It eliminates the need for a dedicated communication module, thereby eliminating the risk of information loss.
• The absence of a wireless communication module reduces the overall system cost.• Sensing primary side current and voltage at high frequencies, such as 100 kHz, is difficult due to the lack of readily available sensors with sufficient bandwidth.
• Indirect control strategies estimate battery current and voltage through mathematical equations rather than direct measurement, which may lead to slight discrepancies between the estimated and actual values.Secondary side direct control • It provides precise and robust performance without the need for communication between the receiver and transmitter.
• This approach facilitates the development of control systems aimed at enhancing efficiency and optimizing power charging.• This control approach results in increased weight and complexity on the receiver side. Secondary side indirect control • It does not require a dedicated communication module, thereby reducing the risk of information loss. • Sensing secondary side current and voltage at high frequencies, such as
100 kHz, is difficult due to the lack of readily available sensors with sufficient bandwidth.
• Indirect control strategies estimate battery current and voltage through mathematical equations rather than direct measurement, which may lead
to slight discrepancies between the estimated and actual values. -
Implementing all four control strategies is technically possible; however, thoroughly addressing them in a single paper is not feasible. Therefore, this paper will concentrate on showcasing the simulation and Hardware in Loop Validation of two specific strategies: primary side indirect control for CC-CV charging of Li-Ion batteries and primary side direct control for CC-CV charging of Li-Ion batteries. The simulation involves an SS-RIPT based charger simulated in PLECS, with parameters outlined in Tables 3 & 4. A comprehensive simulation circuit for the primary side indirect control is illustrated in Fig. 12.
Table 3. Specification of the SS-RIPT-based charger.
Parameters Values Input voltage, Vdc 24 V CV mode voltage, Vbatt,max 4.2 × 5 = 21 V CC mode current, Ibatt 5 A Minimum output voltage, VBatt,min 0.6 × 21 = 12.6 V Maximum output power, Pout 21 × 5 = 105 W Switching frequency, fsw 85 kHz Table 4. Parameters of the SS-RIPT link.
Parameters Values Primary inductance, LP 33.30 μH Secondary inductance, LS 39.73 μH Primary capacitance for 85 kHz, CP 105.27 nF Secondary capacitance for 85 kHz, CS 88.23 nF Mutual coupling 0.20 Figure 12.
PLECS simulation circuit of primary side indirect control of an Li-Ion charger using CC-CV charging.
In Table 2, the CC-CV charging profile has been decided based on 5,200 mAh 5S 25C/50C (18.5 V) Lithium Polymer battery pack[37,38].
In Fig. 12, the RMS value of IP is sensed and used as feedback in the CV controller. For the CC controller, the RMS value of VP is sensed and used as feedback. As stated earlier, the average, RMS, or peak value could be used.
-
This section discusses the simulation of both direct and indirect primary side control methods. The results, exported from PLECS, are plotted in MATLAB for enhanced clarity. The findings are presented in two subsections: Primary side indirect control; and Primary side direct control.
Primary side indirect control
-
In primary side indirect control, the primary side RMS voltage and RMS current are used to control VBatt and IBatt. Adjusting IBattREF modifies VPREF for the voltage controller while adjusting VBattREF modifies IPREF for the current controller.
When IBattREF is changed from 5 to 3 A, the corresponding VPREF is adjusted, and VPRMS accurately tracks this change, as shown in Fig. 13a. Similarly, Fig. 14a demonstrates that VPRMS follows VPREF despite step changes in the load. Figures 13b & 14b illustrate the responses of VP and IP during these transitions.
Figure 13.
Simulation result for voltage controller: (a) step change in IBattREF from 5 to 3 A to change the VPREF, (b) primary side voltage and current waveform for the same.
Figure 14.
Simulation result for voltage controller: (a) change in load from 4.2 to 2 to 5 Ω, (b) primary side voltage and current waveform for the same.
When VBattREF is changed from 21 to 12 V, the corresponding IPREF is adjusted, and IPRMS accurately tracks this change, as shown in Fig. 15a. Likewise, Fig. 16a demonstrates that IPRMS continues to follow IPREF despite step changes in the load. The responses of VP and IP throughout these transitions are shown in Figs 15b & 16b.
Figure 15.
Simulation result for current controller: (a) step change in VBattREF from 21 to 12 V to change the IPREF, (b) primary side voltage and current waveform for the same.
Figure 16.
Simulation result for current controller: (a) change in load from 4.2 to 2 to 5 Ω, (b) Primary side voltage and current waveform for the same.
By replacing the load resistor with a Li-ion battery model designed in PLECS, as shown in Fig. 12, both controllers can operate together using logic to control the CC-CV mode of operation. The resulting performance is illustrated in Fig. 17.
Primary side direct control
-
In the primary side direct control approach, the VBatt and IBatt serve as key feedback inputs for the CC-CV controller. This controller, in turn, orchestrates the generation of the appropriate PWM signals. These signals finely tune the output of the primary side inverter, thereby precisely regulating the voltage and current delivered to the battery, ensuring optimal charging performance.
When VBattREF is adjusted from 21 to 10 V and subsequently to 18 V, the corresponding VBatt accurately tracks these changes, as illustrated in Fig. 18a. Similarly, Fig. 19a shows that IBatt continues to follow IBattREF despite step changes in the load. The responses of VP and IP during these transitions are depicted in Figs 18b & 19b.
Figure 18.
Simulation result for voltage controller: (a) step change in VBattREF from 21 to 10 to 18 V, (b) primary side voltage and current waveform for the same.
Figure 19.
Simulation result for voltage controller: (a) change in load from 4.2 to 8 Ω, (b) primary side voltage and current waveform for the same.
Similarly, when IBattREF is adjusted from 5 to 2 A and subsequently to 4A, the corresponding IBatt accurately tracks these changes, as illustrated in Fig. 20a. Likewise, Fig. 21a demonstrates that IBatt continues to follow IBattREF despite step changes in the load. The responses of VP and IP during these transitions are shown in Figs 20b & 21b.
Figure 20.
Simulation result for voltage controller: (a) step change in IBattREF from 5 to 2 to 4 A, (b) primary side voltage and current waveform for the same.
Figure 21.
Simulation result for current controller: (a) change in load from 4.2 to 3 Ω, (b) primary side voltage and current waveform for the same.
By replacing the load resistor with a Li-ion battery model designed in PLECS, as shown in Fig. 12, both controllers can operate together using logic to control the CC-CV mode of operation. The resulting performance is illustrated in Fig. 22.
-
The proposed control strategy is validated through Hardware-in-the-Loop (HIL) simulation using Typhoon HIL, as illustrated in Fig. 23. A digital twin of the RIPT system is developed in Typhoon HIL, with the controller implemented on a Texas Instruments TMS320F28335 DSP. The results obtained from the Typhoon HIL simulation are exported and plotted in MATLAB for enhanced clarity.
Primary side indirect control
-
Figures 24 & 25 display the HIL results for the voltage controller validation, demonstrating strong agreement with the simulation results depicted in Figs 13 & 14 from PLECS. Similarly, Figs 26 & 27 exhibit the HIL results for the current controller, which closely align with the PLECS simulation results shown in Figs 15 & 16.
Figure 24.
HIL result for voltage controller: (a) step change in IBattREF from 5 to 3 A to change the VPREF, (b) primary side voltage and current waveform for the same.
Figure 25.
HIL result for voltage controller: (a) change in load from 4.2 to 2 to 5 Ω, (b) primary side voltage and current waveform for the same.
Figure 26.
HIL result for current controller: (a) step change in VBattREF from 21 to 12 V to change the IPREF, (b) primary side voltage and current waveform for the same.
Figure 27.
HIL result for current controller: a) change in load from 4.2 to 2 to 5 Ω, (b) primary side voltage and current waveform for the same.
Primary side direct control
-
Figures 28 & 29 present the HIL results for the voltage controller validation, showing a strong correlation with the simulation results from PLECS depicted in Figs 18 & 19. Similarly, Figs 30 & 31 display the HIL results for the current controller, which closely align with the PLECS simulation results shown in Figs 20 & 21.
Figure 28.
HIL result for voltage controller: (a) step change in VBattREF from 21 to 10 to 18 V, (b) primary side voltage and current waveform for the same.
Figure 29.
HIL result for voltage controller: (a) change in load from 4.2 to 3 to 8 Ω, (b) primary side voltage and current waveform for the same.
Figure 30.
HIL result for voltage controller: (a) step change in IBattREF from 5 to 2 to 4 A, (b) primary side voltage and current waveform for the same.
Figure 31.
HIL result for current controller: (a) change in load from 4.2 to 2 to 3 Ω, (b) primary side voltage and current waveform for the same.
A model of a Li-ion battery was created in PLECS to validate the CC-CV charging technique. The emphasis during the HIL simulation was placed on showcasing how the system adapts to changing loads, thereby underlining the effectiveness and dependability of the implemented control approach.
-
In conclusion, wireless power transfer, particularly through resonant inductive power transfer (RIPT), is gaining momentum as a convenient and efficient method for charging a variety of devices including Electric Vehicles (EVs), Unmanned Aerial Vehicles (UAVs), and consumer electronics such as cell phones. This technology not only provides a safe and efficient charging experience but also addresses issues such as range anxiety in EVs and extending the flight time of UAVs by eliminating the need for constant user intervention during charging. Moreover, the absence of charging cables reduces clutter and keeps charging areas organized for consumers.
The paper reviewed control methods applicable to RIPT systems for charging batteries using the Constant Current Constant Voltage (CC-CV) mode, focusing primarily on the series-series RIPT (SS-RIPT) system. It presented various control strategies, including direct and indirect control methods, and discussed their implementation for both primary and secondary sides of the RIPT system. While acknowledging the widespread use of bidirectional power transfer, the paper concentrated solely on unidirectional power transfer and left bidirectional control for future research.
This paper primarily addresses the details of primary side indirect and primary side direct control for CC-CV charging of Li-ion batteries. Both control strategies were simulated using PLECS and verified through HIL results with the DSP controller TMS320F28335 and Typhoon HIL. The feasibility and effectiveness of both controls were demonstrated through simulations and analysis, providing valuable insights for practical implementation.
Overall, this study contributes to the understanding of control strategies for RIPT systems, particularly in the context of CC-CV charging, and provides a foundation for further research and development in this field. As wireless power transfer continues to evolve, such studies are crucial for optimizing charging efficiency, improving user experience, and advancing the adoption of wireless charging technology across various applications.
-
The authors confirm contribution to the paper as follows: study conception and design: Munsi A, Pradhan S; data collection: Munsi A, Pradhan S; analysis and interpretation of results: Munsi A, Pradhan S, Aditya K; draft manuscript preparation: Munsi A, Aditya K. All authors reviewed the results and approved the final version of the manuscript.
-
All data included in this study are available upon request from the corresponding author.
This research work is funded by the SEED Grant, IIT Jodhpur with grant no: I/SEED/KUA/20220126.
-
The authors declare that they have no conflict of interest. Kunwar Aditya is the Editorial Board member of Wireless Power Transfer who was blinded from reviewing or making decisions on the manuscript. The article was subject to the journal's standard procedures, with peer-review handled independently of this Editorial Board member and the research groups.
- Copyright: © 2024 by the author(s). Published by Maximum Academic Press, Fayetteville, GA. This article is an open access article distributed under Creative Commons Attribution License (CC BY 4.0), visit https://creativecommons.org/licenses/by/4.0/.
-
About this article
Cite this article
Munsi A, Pradhan S, Aditya K. 2024. Perspectives on control strategies for CC-CV charging in Resonant Inductive Power Transfer systems: a review of SS-RIPT configuration. Wireless Power Transfer 11: e009 doi: 10.48130/wpt-0024-0009
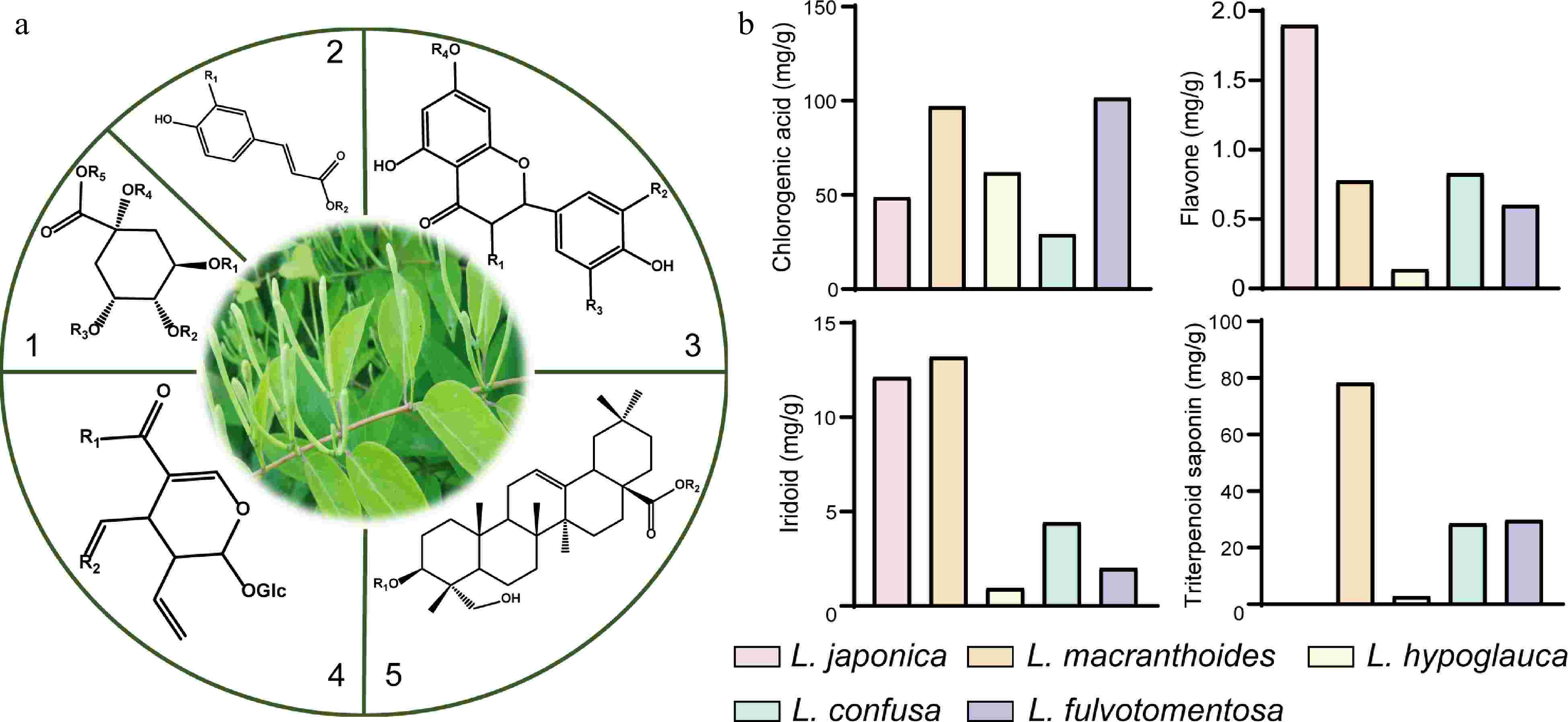