-
Energy has been the biggest problem of humankind since its existence. This process, which started with the discovery of fire, has evolved to the present day. While fuels (wood, coal, etc.) were initially used as energy sources, oil and its derivatives were added to these with industrial development. Since the damage to the ecosystem has increased worldwide and we have begun to confront this, resources with high carbon emissions, such as fossil fuels, have begun to be replaced by renewable and less harmful resources. Similarly, fossil fuels are the most used and most accessible fuel for vehicles. Apart from this, gases such as LPG are also used in vehicles as an energy source. When looking at alternative fuel vehicles, the fuel cells convert chemical energy into electrical energy. Although ethanol and methanol can be fuel cell fuel, hydrogen is most commonly used. This technology can be used not only in transportation but also in storage and charging units. The local emissions produced by fuel cells while in use are almost zero. These days, when the world is trying to follow a more environmentally friendly approach, developing fuel cells can help reduce the rate of global warming.
Hydrogen has properties that require extreme attention, such as being stored under high pressure, the risk of leakage due to its small molecular structure, high flammability, and the heat and flame released as a result of combustion being difficult to control. Appropriate storage systems and safety measures are essential to ensure the safe handling and use of hydrogen.
Vapor Cloud Explosions (VCE) caused by hydrogen and hydrocarbon-based mixtures have occurred in chemical plants, nuclear power plants, and refineries. The number of these explosions has increased recently. Therefore, the requirement to model explosions has emerged. VCE accounts for 40%−65% of all explosion-related industrial accidents. A methodology for the consequential analysis of compressed hydrogen releases considering various event escalation stages, including high-pressure gas release, gas jet dispersion, and overpressure considerations, was established by Sun & Loughnan[1]. The conceptual nozzle theory was revised to address the flow regime transition and input to the CFD (Computational Fluid Dynamics) model for gas jet dispersion. The model was validated with experimental results, achieving a less than 20% deviation[1]. Johnson et al. focused on large-scale VCE experimental studies spanning five decades. The importance of congestion and confinement was demonstrated, and it was stated that hydrogen exhibited differences among various hydrocarbons that should not be underestimated[2]. Some of the most widely accepted theories about VCE based on classical acoustic theory and pressure wave propagation models were investigated by Salzano[3]. A consequence-based threshold (minimum) value for the critical hydrogen mass needed at a stoichiometric concentration in the air for a vapor cloud to behave as VCE was determined. It was stated that the results can be used for both compressed and cryogenic liquid tanks[3]. An integrated approach composed of RSM (Response Surface Analysis) and MPACT models was used to predict fatality rates caused by benzene emitted from floating-roof tanks by Barjoee et al.[4]. RSM scenarios were configured in Expert Design (version 7.0) software using the CCD (Central Composite Design) method, and five variables of wind speed, relative humidity, atmospheric temperature, failure diameter, and emission height were considered[4]. VCE hazards associated with very lean hydrogen-air mixtures (≤ 14% H2) were investigated by Malik et al.[5]. Flame velocities and explosion loads were measured using high-speed video and a series of dynamic pressure transducers. The test setup and results were discussed, including a comparison with data from previous tests. The measured flame velocities were compared with those predicted using computational fluid dynamics analysis[5]. A study of the assumptions and simulation techniques used to reduce the computational costs associated with gas explosion modeling for each different explosion type was conducted by Shamsuddin et al.[6]. The numerical explosion models were categorized into basic and advanced CFD models. It was stated that the categorization should be done considering the complexity of the explosion geometry used in the analysis[6]. Hu et al. conducted a systematic review of hydrogen explosions[7]. Potential explosion scenarios, including the presence of impurities and a rich oxygen environment in the production, ultra-high pressure, and ultra-low temperature storage, transportation, and consumption processes, were investigated[7]. In the study by Wang et al., experimental studies were performed on critical parameters such as tank explosion pressure, explosion temperature, liquid filling rate, and tank volume that cause VCE[8]. It has been emphasized that BLEVE is a significant factor that triggers VCE[8]. CFD was used to model VCE in two industrial accidents (Amuay Refinery Disaster in 2012 and Indian Oil Corporation (IOC) Jaipur Terminal Disaster in 2009) by Sajid et al.[9]. It was stated that the simulation of different scenarios can help develop and improve safety guidelines to reduce similar accidents[9]. The study by Shi et al. aimed to evaluate the flame speed for the Barker-Strehlow-Tang (B-S-T) method in VCE[10]. The 100 biggest accidents in hydrocarbon processing in the powder industry between 1957 and 1986 were examined, and it was determined that 42% of the accidents were caused by VCE[10]. In the study by Ahumada et al., the onset of VCE was predicted using the B-S-T model. It was observed that the flame speed was underestimated, and the value estimated in the overpressure calculation differed from the value found as a result of the experiment[11]. A violent, episodic vapor cloud explosion assessment based on the deflagration-to-detonation transition was analyzed by Sharma[12]. It was stated that vapor cloud explosion could not be caused by deflagration alone, given the widespread occurrence of high overpressures and direction indicators in open and uncongested areas containing the cloud[12]. According to the post-accident investigation of the current accident case, Wang et al. conducted an integrated analysis of the fireball characteristics and thermal damage during the explosion accident. An optimized model for the fireball characteristics was developed based on full-scale experimental verification. It was found that the optimized model could facilitate better predictions of detailed parameters from the fireball of LNG (Liquefied Natural Gas) VCE[13]. Niazi et al. proposed a grid-based dynamic risk analysis framework to analyze the impact of VCEs on human fatality risk on the coastal platform. CFD was used to model VCEs by accounting for different wind and leakage conditions. Bayesian Inference (BI) was also performed using Accident Sequence Predictor (ASP) data to estimate the dynamic risk. It was determined that increasing the leakage rate for a given wind speed reduced the human fatality risk[14]. Oran et al. presented information on the basic mechanisms of flame acceleration and DDT (Deflagration to Detonation Transition), which were then compared with explosion evidence (explosion markers) from large-scale tests and actual large vapor cloud explosions (VCEs), including the incidents at Buncefield (UK), Jaipur (India), CAPECO (Puerto Rico), and Port Hudson (USA). The most important conclusion from this review is that detonations have occurred in at least some of the VCE accidents before VCEs[15]. Gill et al. used commercially available electrical control boxes, 600 mm height, 400 mm width, and 250 mm depth, with doors provided as aluminum foil and vent covers to investigate the pressure development, venting processes, and flame characteristics of stoichiometric propane/air explosions. Maximum pressure was reached one-third of the time with the addition of congestion[16]. The B-S-T method stands out in the analysis of vapor cloud explosion hazards. The study by Alexeev et al. examined the vapor cloud explosion caused by hazardous chemicals formed during waste processing in the coke production plant using the B-S-T model. In the most current version, the BST2 method, a new matrix was used with the BST1 nomogram[17]. In the study conducted by Li & Hao, flue gas explosions in storage tanks were tested, and the calculated far-field pressure consequences were compared with B-S-T model predictions. Stoichiometric mixtures of methane and air were used in the tests[18]. The study by Wesevicha et al. aimed to evaluate the vapor cloud explosion loads occurring in facilities accurately and efficiently using the B-S-T method to design effective and low-cost improvements. For this purpose, a vapor cloud explosion scenario occurring in the oil refinery building was prepared. The first step estimated pressure and impulse for an obstacle-free region using the B-S-T method. In the second step, the vapor cloud explosion source was developed. A peak pressure of 3.01 psi and a peak impulse of 0.12 psi were produced at 65 m from the center of the vapor cloud[19].
In addition to correlations, consequences analysis is also performed using various software, especially the free ALOHA Software. A consequence analysis was performed with accident scenarios related to different sources of H2S gas by Cetinyokus[20]. ALOHA and EFFECTS were used for the analysis. Acetone and butyl acetate were extracted from the hardwood furniture business and were analyzed with ALOHA Software by Changphuek et al.[21]. The consequences of chlorine gas release from a reactor were performed with numerical calculation methods and with the ALOHA by Chehrazi et al.[22]. Accident scenarios were created based on the natural gas distribution pipeline fire that occurred in Istanbul on April 28, 2020, and the threat zones of the jet fire were calculated with the ALOHA Software by Besiktas et al.[23]. A case study for the consequences of an industrial accident in a fuel station was analyzed with ALOHA Software by Cetinyokus & Pamuk[24]. Apart from ALOHA, other software tools are also used in modeling studies. In the study conducted by Barjoee et al., the effects and consequences of toluene release in various scenarios were modeled through ALOHA and PHAST programs. The highest probability of death was 92%, and it occurred at a distance of 1 m during the cold season. The output values for the PHAST program were higher than those of ALOHA[25]. P-xylene and O-xylene leakage from storage tanks were modeled with ALOHA and WISER (Wireless Information System for Emergency Responders) by Barjoee et al. It has been shown that creating a protective zone of 54 m radius around P-xylene and O-xylene tanks is necessary.[26]. In another study conducted by Barjoee et al., the hazard radius of benzene release from the tank of one of the coking and tar refining industries was evaluated using ALOHA. The toxic vapor cloud of benzene covered parts of the adjacent coke plant, but the flammable vapor cloud did not reach adjacent industries[27]. The consequences of accidents related to atmospheric storage tanks in a petrochemical plant were investigated with PHAST 8.22 Software by Rashidi & Varshosaz[28]. Two factors affecting the consequences of toxic substances were determined: the inhaled substance's concentration and the inhalation duration[28]. The results of all these studies provide useful information for designing the site and the emergency response plan.
Hydrogen and fuel cells have recently been widely used to meet the world's energy demand. The energy intensity of pure hydrogen is 236 times greater than a battery. A fuel cell is a technology that electrochemically converts hydrogen into electrical energy with 50% efficiency. Although hydrogen has high energy per unit mass, it has very low energy content per unit volume compared to liquid fuels and natural gas at room temperature and atmospheric pressure. Therefore, it is usually compressed or liquefied by reducing its temperature below 33 K. Operating conditions are hazardous because hydrogen requires high pressure and liquid storage conditions. Hydrogen has a very wide flammability range (4%−74% in air, 4%−94% in oxygen by volume), and it is significant to prevent air or oxygen from mixing with hydrogen, especially in closed spaces. Also, hydrogen tends to leak easily. Therefore, these dangers of hydrogen must be minimized. This study analyzed the possible effects of a release in the hydrogen storage tank during hydrogen fuel cell production in a sample industrial facility's laboratory. Jet fire and no fire due to the release were considered. The consequences were analyzed using the ALOHA Software and the B-S-T method. ALOHA is a widely used free hazard modeling program for planning and responding to emergencies. ALOHA generates threat zone estimates for various hazards by entering the details of an actual or potential chemical release. It has a valuable database of over 1,000 chemicals and is practical to use with its user-friendly interface. It can also provide GIS-based credits. Due to these advantages, the ALOHA software was used in the present study. Research on hydrogen tank explosions in fuel cell production facilities have been analyzed using different methods in the literature. However, this study is the first to combine ALOHA software and the B-S-T method. In addition, it is the first study conducted on hydrogen tank explosions in a fuel cell facility in Türkiye.
-
The first chemical property of hydrogen discovered is that it forms water (H2O) by flammable reaction when combined with oxygen. Nearly all of the hydrogen on Earth exists in molecular form, such as water or organic compounds, as it forms covalent compounds with most nonmetallic elements. Its chemical formula is H2 and its CAS-Number is 1333-74-0[29].
Hydrogen is a highly flammable hazardous chemical showing flammability: 4 hazard classes (Fig. 1). Important physical and chemical properties of hydrogen are presented in Table 1.
Table 1. Physical and chemical properties of hydrogen[29].
Physical state Gas Form Compressed gas Color Colorless Smell Odorless Melting point −259.2 °C Boiling point −253 °C Critical temperature −240.0 °C Flammability Flammable gas Flammability upper value 74.2% (V) Flammability lower value 4% (V) Vapor pressure 165,316.8 kPa (25 °C) Humidity 0.069 Relative humidity 0.07 Solubility in water 1.62 mg/L Auto-ignition temperature 560 °C Hydrogen is dangerous due to its physical properties, such as high burning rate, low ignition temperature, and low flammability limit. The ignition temperature of hydrogen is lower than that of many other types of gases. Under normal atmospheric conditions, hydrogen concentrations between 4% and 74% with air can form an explosive mixture. Therefore, using or storing hydrogen in a confined space without ventilation is dangerous. The flammability of hydrogen is also a hazard. Once ignited, the flame can spread quickly and pose an explosion hazard. Additionally, when hydrogen burns, a blue flame emits high temperature and intense light. Therefore, it should be taken into account that if hydrogen burns, the flames can be so bright that they can temporarily blind the eyes.
Hydrogen storage tank characteristics
-
The hydrogen storage tank specifications specified in the scenario could not be achieved for the hydrogen storage tank in the sample defense facility or another facility producing fuel cells throughout Türkiye. For this reason, locations where fuel cell production and hydrogen storage tanks are used have been researched worldwide. Analyses was carried out considering the hydrogen storage tank properties specified by Cui et al.[30] (Table 2).
Table 2. Hydrogen storage tank specifications[30]
Parameter Value Nominal volume (L) 140 Pressure (atm) 345 Temperature (°C) 24 Orientation Vertical Diameter (m) 4.03 Length (m) 10.98 Tank type Cylinder The high-pressure gaseous hydrogen storage tank included in the study has the most widespread use because it has a simple structure and fast charging and discharging characteristics, which is suitable for hydrogen use. Since the density of hydrogen is low, the design pressure of gas storage tanks generally reaches 35 MPa or even 70 MPa to improve the volumetric energy density of hydrogen tanks[7].
Analysis
-
The B-S-T method and ALOHA software were used to determine the explosion effects caused by release in the hydrogen storage tank. Two scenarios were studied in the software, and possible physical impact areas were determined.
Analysis using the B-S-T method
-
The B-S-T method was developed to estimate the overpressure (positive and negative pressure waves) and impulse coefficient resulting from VCE. The method assumes that only congested or partially confined parts of the flammable vapor cloud contribute to overpressure accumulation, and the explosion energy (E) is estimated. A curve determines Ps as the combustion energy scaled distance function in the B-S-T method. Numerically determined pressure and impulse coefficient curves taking the flame Mach number as parameters are also used[31].
The Baker-Strehlow-Tang method calculates the scaled distance (Eqn 1).
dn=dM1/3 (1) dn is the ratio of the distance from the explosion center to the point where the estimated overpressure should be calculated to the cube root of the charge masses (m kg−1/3). Here, d is the actual distance, and the mass value of the explosive is M (kg). The cube root of the charge masses at the explosion center is often used as a scaling parameter. When two explosives with similar geometry but different dimensions explode in the same atmosphere, similar peak overpressures are produced at the same scale distance. This is the simplest and most common form of explosion scaling. Another approach suggested by Sachs is the one that will be used below. The blast wave can be expressed as a scaled overpressure function and is calculated by Eq. (2)[31].
ΔPs=PsP0 (2) where, P0 is the atmospheric pressure (Pa), and ΔPs is the peak overpressure (Pa).
Combustion energy is calculated by scaled distance (or Sachs scaled distance) (Eqn 3).
R=d(E/P0)1/3 (3) where, R is scaled distance (m), and E is explosion energy (J).
Analysis with ALOHA software
Location and chemical selection
-
The analysis was performed at a defense industry company in Ankara (Türkiye), which houses a hydrogen storage tank for fuel cell production.
Atmospheric conditions
-
Modeling studies were conducted in summer conditions to predict more considerable impact distances. Due to higher atmospheric mean temperature in warm seasons, ambient saturation concentration and vapor pressure are higher[26]. June was chosen to represent summer conditions. Summer conditions were chosen for the accident scenario because, in hot weather, hydrogen gas molecules in the air move more and disperse faster. This may cause hydrogen gas to mix with air quickly and react more easily with oxygen. The atmospheric conditions of Ankara province for June are given in Table 3.
Table 3. Atmospheric conditions of Ankara province in June[32].
Parameter Value Air temperature 24 °C Wind speed 3 m/s Wind direction Northwest Cloudiness Open Relative humidity 40% Surface roughness Low Atmospheric stability D Low wind speeds have been shown to account for over 70% of accidents involving VCEs. Low wind speeds cause fuel leakage due to gravity and are associated with massive clouds with a much higher ignition risk[9].
Scenario selection
-
Based on past accident data, it was assumed that the release occurred due to the rupture of the 4.26 cm diameter pipe connected to the hydrogen storage tank. Analyses were performed using two different scenarios, which are listed below:
Scenario 1: No fire due to release;
Scenario 2: Jet fire due to release.
Because ALOHA is limited to chemicals that become airborne, it includes models to evaluate the rate at which a chemical will be released and volatilized from the congestion. These 'source strength' models can be critical components in assessing hazards. ALOHA couples source strength models to a dispersion model to estimate the spatial extent of toxic plumes, flammable vapors, and explosive vapor clouds. However, ALOHA does not model all combinations of source strength, scenario, and hazard category for combustion scenarios. The user must select a specific combination from a limited selection. ALOHA uses LOC (Levels of Concern) to address the impact of toxic air plumes, fires, and explosions on human populations. For inhalation hazards, ALOHA's LOCs are concentrations of airborne chemicals associated with adverse health effects. Because ALOHA is primarily used in situations where the goal is to assess the threat a chemical release poses to the general public, it includes LOCs specifically designed to predict how the general public will respond to a short-term release. In limited cases, exposure guidelines developed for worker safety are also compiled and provided to users as an option. The impact intensity of the ALOHA Software decreases in the red, orange, and yellow threat zone order. For toxic inhalation hazards, LOCs are chemical-specific. Thresholds for inhalation toxicity are derived from CAMEO Chemicals. AEGLs (Acute Exposure Guidelines), ERPGs (Emergency Response Planning Guidelines), PACs (Protective Action Criteria), and IDLH (Immediate Danger to Life and Health) limits are stored in data files integrated into ALOHA.
ALOHA models only combustion reactions. ALOHA predicts the blast wave from vapor cloud explosions that are not fully or partially confined by confining walls or ceilings (rapid deflagrations and detonations). Confined vapor cloud explosions produce more damaging blast waves than non-confining or partially confining explosions. The B-S-T model forms the basis of the ALOHA overpressure calculation[33]. The overpressure is estimated using dimensionless, experimentally derived detonation curves based on the flame front propagation velocity and the fuel mass involved in the reaction. The basic principle of this method is the existence of regions within the vapor cloud where physical structures can increase the flame front velocity. These regions are characterized by the structure intensity using a parameter called congestion. Flame velocity is related to the chemical properties of the fuel, the degree of congestion, and the nature of the ignition source. A reactivity term is used to characterize the chemical properties of the fuel. Reactivity ratings are classified according to the chemical laminar burning velocity in the B-S-T method. Low-reactivity chemicals have velocities of less than 45 cm s−1. High reactivity applies to chemicals with a burning rate greater than 75 cm s−1, and those in between are classified as having medium reactivity. Although some chemicals in the ALOHA database are classified according to these criteria, most flammable chemicals in ALOHA are not classified. ALOHA uses medium reactivity in this case because most chemicals do not exceed 75 cm s−1 in laminar burning. ALOHA's method for estimating normalized pressure as a function of distance from the center of the explosive cloud is built on a series of experimentally determined graphs. B-S-T reports pressure values as a function of normalized distance from the center of the congested region, along with different graphs for different flame speeds. For the application of these graphs in ALOHA, the graph data reported by B-S-T was fit to different functions[34].
ΔPPatm=Difx<x0 (4) elseΔPPatm=A.B1/2⋅xC (5) Here ∆P is the maximum overpressure, and A, B, C, D, and x0 are constants. The normalized distance, x, is defined as:
x=r(PatmE)1/3 (6) Patm is the atmospheric pressure, and r is the distance from the center of the exploding cloud. The energy contributed to the blast wave is:
E=ref.HcMass (7) Here, ref is a ground reflection factor, Hc is the fuel's combustion heat, and Mass is the mass of the fuel involved in the explosion. In ALOHA, the reflection factor is set to 2 by B-S-T. This takes into account the reflection of the blast wave from the ground. ALOHA's method is based on a simple conceptual model of the explosive cloud. The cloud is treated as a hemisphere with a uniform ground-level concentration. Higher clouds have a smaller reflection factor.
The most crucial difference between the B-S-T method and ALOHA is determining the mass of fuel contributing to the explosion. In the B-S-T method, the mass of fuel contributed to the explosion is determined by the mass of the compressed areas in a combustible cloud. From the ignition point, the flame travels to the compressed areas, accelerating and decelerating in the uncompressed areas. The mass of fuel contributing to the explosion is simply the mass of fuel in a compressed area. A combustible cloud from a single release can cause as many explosions as there are different compressed areas. Flame velocities are determined by the levels of compression in these areas. In uncompressed areas, the flame speed is assumed to be so slow that it does not produce a significant pressure increase. ALOHA uses a different approach to determine the mass of the fuel causing the explosion, based on recommendations from the American Institute of Chemical Engineers. AIChE recommends that B-S-T detonation curves be combined with an air distribution model to determine the mass of the explosive cloud and that all fuel within the explosive limit be multiplied by an efficiency factor. An efficiency factor of 5% to 20% is recommended, with ALOHA using 20%. ALOHA deviates slightly from AIChE recommendations by using fuel in the concentration range between the upper explosive limit and 90% of the lower explosive limit. This minor change is included in ALOHA to create another protective line in the hazard zone calculation. In ALOHA, referred to as 'hard ignition', or if the average intensity level shows a transition to detonation, 100% of the explosive cloud is used, and Mach 5.2 is used for the flame speed[34].
ALOHA uses a solid flame model to calculate jet-fire thermal radiation hazards. The thermal radiation impinging on a distant target is calculated from the product of the thermal radiation flux at the fire surface, the geometric viewing factor, and the thermal radiative transmittance factor of the atmosphere.
q=E.F.ℸ (8) where q is the thermal radiation flux incident on a vertical surface (W m−2), E is the thermal radiation energy flux at the surface of the fireball (W m−2), F is the geometric view factor, and
is the transmissivity of the atmosphere to thermal radiation.ℸ Chamberlain's formula is used in ALOHA to determine the flame height of a gas released from a tank. The effect of wind is integrated into the thermal radiation component, the geometric view factor, by correlations. The effects of thermal radiation are a function of the energy flow and the exposure time. For fires exceeding 30 s, the LOC is based on the thermal radiation produced by the flame[34].
-
Empirical formulas derived from the best experimental data have been applied to predict hydrogen explosion overpressures, and theoretical derivation and design guidelines for flammable gases and explosives have also been transferred and used for hydrogen explosion overpressure predictions. In engineering applications, there are three traditional approaches widely used to estimate the blast load of VCE: the TNT equivalent method (TNT-EM), the TNO multiple energy method (TNO-MEM), and the Baker-Strehlow-Tang method (B-S-T). TNT-EM converts the released energy of the explosive into the charge energy of TNT in an explosion. TNO-MEM considers the strength of the vapor cloud explosion depending on the boundary conditions, which assumes that the unconstrained part of the vapor cloud contributes little to the blast intensity. The BST method considers different flame speeds of different explosives or VCEs, but is generally similar to TNO-MEM[35,36]. In the B-S-T method, the curve is used to determine the peak pressure (Fig. 2).
Figure 2.
Variation of peak pressure with combustion energy scale distance for different Mach numbers[31].
The strength of the blast wave is proportional to the maximum flame speed in the cloud. The flame Mach number is the apparent flame speed divided by the ambient speed divided by the speed of sound. The appropriate Mf (Mach number) for each modeled case can be selected from Table 4.
Table 4. Mach numbers used in the B-S-T method[31].
Flame expansion Reactivity Congestion Low Medium High 2D High 0.599 DDT DDT Medium 0.47 0.66 1.6 Low 0.079 0.47 0.66 2.5D High 0.47 DDT DDT Medium 0.29 0.55 1.0 Low 0.053 0.35 0.50 3D High 0.36 DDT DDT Medium 0.11 0.44 0.50 Low 0.026 0.23 0.34 In Table 4, no plane limiting flame expansion is considered 3D. The presence of a single limiting plane means 2D flame expansion. Congestion category 2.5D corresponds to situations where the confinement is made either of a frangible panel (which can be expected to fail rapidly and provide ventilation) or a nearly solid confinement plane. Congestion is considered low if the area occupancy rate is below 10%, medium if between 10% and 40%, and high if above 40%. Hydrogen is a highly reactive, highly dispersive gas. Considering the sample plant layout, congestion is selected as low. Considering the low congestion, high reactivity, and 3D propagation, the Mf was determined as 0.36 from Table 4. Calculations were made using the specified correlations and values (Eqns 1−3). The explosion energy E = 154,308 × 106 J was calculated by multiplying the 44,088 m3 (3,968 kg) release gas volume by 5 × 106 J m−3. The scaled distance (R) was obtained as 1.8 at the target distance of 207 m. The dimensionless peak pressure (∆Ps) was determined as 0.06 from the curve in Fig. 2. The peak pressure (Ps) was calculated as 6,079.5 Pa by multiplying this value by the atmospheric pressure (P0). When the vulnerability that the peak pressure would create was interpreted, it was revealed that this pressure would shatter windows and glass[13].
As an active, flammable chemical, hydrogen has a high risk of deflagration and explosion. Post-incident investigations have shown that 20% of the losses in hydrogen accidents are due to fire, while more than 75% are due to explosion. The overpressure in explosions can vary from close to zero to several bars. The threshold value for a safety distance is 2.07 kPa, below which the probability of no severe damage to property is stated to be 0.95%[7].
Traditional methods are designed for a symmetric barrier-free environment, which differs from the specific scenario of hydrogen explosions in confined space. Moreover, hydrogen is more active than traditional flammable gas, which releases more energy and thus produces higher explosion pressure. The existing TNO MEM and BST model parameters for hydrocarbon fuels may not be suitable for hydrogen[7]. The approach, which combines empirical and CFD methods in a balanced way, can provide a tool for more accurate and practical risk assessment related to hydrogen release[1].
Analysis with ALOHA software
-
Damage in VCE is related to the shape and size of the blast wave. Peak overpressure and impulse are often used to characterize the blast wave. ALOHA uses only peak pressure to characterize detrimental effects due to the blast wave. The explosion threat zone of the vapor cloud obtained with Scenario-1 is given in Fig. 3.
The chemical mass in the tank is 3,995 kg. The release time is 23 min. The maximum release rate is 971 kg min−1, and the total amount released is 3,968 kg. Red and orange threat zones could not be determined because the exposure limit value was not exceeded in the ALOHA Software. An impact distance of 207 m from the source was determined for the yellow threat zone (> 1.0 psi). In a possible accident scenario, a pressure greater than 1.0 psi will be felt due to the explosion, and the windows of buildings within 207 m will be broken. A Google Earth image of the explosion effect is given in Fig. 4.
Figure 4.
Google Earth image of the explosion threat zone of the vapor cloud for hydrogen storage tanks (Scenario -1).
The hydrogen tank is stored in a closed environment inside the building. For this reason, threat zones are shown in the building where the tank is located. Since the sample facility is located in an industrial area, many facilities are around it. Since the facilities are very close, domino effects can be seen inside and outside the facility. As a result of a possible explosion, the battery factory near the facility may also be affected. Batteries or other flammable materials inside the facility may catch fire, and the fire may spread rapidly. There are also residential areas near the facility. People around may be harmed. Chemicals released due to the explosion can cause water pollution and damage the ecosystem. It is essential to eliminate or minimize this impact in emergency plans. It is challenging to mitigate the hydrogen explosion in the event of a leak by eliminating ignition sources. In addition, due to the minimal ignition energy, when hydrogen is released at high pressure, the strong shock wave generated by the high-pressure hydrogen jet can cause hydrogen to ignite spontaneously. The minimum ignition energy required by the hydrogen-air cloud is affected by the ambient temperature, which decreases as the temperature increases[7]. Other threat zones identified within the scope of Scenario-1 are given in Fig. 5.
Figure 5.
(a) Flammable threat zone of vapor clouds. (b) Toxic threat zone of the vapor cloud for hydrogen storage tanks (Scenario-1).
The toxic threat zone represents the region where the vapor cloud contains chemicals that have toxic effects. AEGLs, ERPGs, and PACs are level public exposure guidelines developed for accidental chemical release events. Although developed by different organizations, all three exposure guidelines share the approach of assessing the effects of chemical exposure by using levels to define increasing severity associated with increasing concentration. Toxic effects that may harm human health may occur in this zone due to inhalation or contact with vapor. Two factors affect the consequences of inhaling toxic substances. The first is the concentration of the inhaled substance, and the second is the duration of inhalation[28]. The largest impact distance in the toxic threat zone was seen in the yellow region, 130 m (> 65,000 ppm, PAC-1) away from the source. Lethal effects were observed at a distance of 52 m (> 400,000 ppm, PAC-3) from the source. Atmospheric conditions and emission height in accident scenarios are important variables that determine the size of the toxic vapor cloud[4]. Atmospheric stability refers to the stability of the vertical movement of air masses. In simpler terms, it indicates how strong or weak the tendency of an air mass in the atmosphere to rise or fall is. The D-class stability selected in the study generally refers to a stable air mass in the atmosphere. The flammable threat zone of the vapor cloud refers to the zone where the vapor cloud has flammable properties. In this zone, there may be a risk of burns and explosions if the steam comes into contact with an ignition source. In the flammable zone analysis, 60% of the lower flammability limit is used as the level of concern. It was observed that lethal effects may occur 301 m (> 24,000 ppm, 60% LEL: Flame Pockets) away from the source. Wind direction confidence lines around the threat zone, and approximately 95% of the chemical plume is expected to remain contained[25]. The Google Earth image of the flammable area of the vapor cloud where the largest effects were observed is given in Fig. 6.
Figure 6.
Google Earth Image of the flammable threat zone of vapor clouds for hydrogen storage tanks (Scenario-1).
From Fig. 6, it can be seen that thermal radiation may affect the facilities and settlements. Hydrogen has a wider flammable concentration range than most hydrocarbons. The flammability limit range is greater when a hydrogen flame propagates upward than when it propagates downward. Factors such as temperature, pressure, the presence or absence of diluent, and the structure's shape can all affect hydrogen's flammability limits. Hydrogen can only ignite when the ignition energy is greater than the minimum ignition energy. The minimum ignition energy of hydrogen in air is 101.3 kPa and less than 0.02 MJ at ambient temperature. Therefore, hydrogen can ignite in the presence of any weak ignition source (electric spark, hot surface, open flame, etc.) or even static electricity from the human body (up to 8.33 MJ)[7].
The thermal radiation threat zone determined according to Scenario-2 is given in Fig. 7.
The maximum flame length is 9 m, and the burn lasts 23 min. The effects of thermal radiation are a function of energy flow and exposure time. The effect of thermal radiation on humans depends on the exposure time and radiation intensity. ALOHA calculates the energy flux associated with radiation as a function of distance and fire duration. The impact distance to the red threat zone is 40 m (> 10 kW m−2), and the effect of thermal radiation is considered lethal. The impact distance for the orange threat zone is 56 m (> 5 kW m−2), and second-degree burns may occur as a consequence; the impact distance for the yellow threat zone is 87 m and may cause pain (> 2 kW m−2).
All impact distances determined for the scenarios are given briefly in Table 5.
Table 5. All impact distances for scenarios used in the present study.
Scenario Zone Red threat zone (m) Orange threat zone (m) Yellow threat zone (m) Scenario-1: No fire due to release Toxic threat zone 52 69 130 Flammable threat zone 301 − 711 Explosion threat zone − − 207 Scenario-2: Jet fire due to release Thermal radiation threat zone 40 56 87 As a result of the release of the chemical without burning (Scenario-1), a toxic zone, a vapor cloud flammable zone, and a vapor cloud explosion zone were detected. With Scenario-2, the thermal radiation threat zone was obtained due to a jet fire. The largest impact distance for the hydrogen storage tank was determined for the flammable threat zone of the vapor cloud where there was no fire due to release. It has been seen that it is necessary to create a protective zone around the hydrogen tank to reduce the hazards. It is known that the protective zone distances are different for each chemical. These distances vary depending on the degree of danger of the chemical, its physical and chemical properties, vapor movement, or momentum speed[37,38]. In terms of the affected population, factors such as the number of people, distance from the tank, shelter, operator intervention, etc., gain importance[39,40]. The use of personal protective equipment, training, etc., and strategies for employees within the threat zones estimated by ALOHA, can be applied to reduce the loss of life[27].
The vapor cloud explosion threat zone refers to the potentially explosive region of the vapor cloud. An explosion may occur in this region when explosion pressure and ignition conditions are met. ALOHA includes three LOCs that quantify indirect and direct effects. Glass windows can break above 1 psi, and at 3.5 psi, severe injuries from eardrum rupture and flying debris can occur. At 8 psi, the risk of ear and lung damage and indirect effects due to the collapse of unreinforced buildings becomes significant. For the yellow threat zone, it has been determined that the windows of buildings can be broken by the explosion effect (1 psi) in the impact distance 207 m away from the source. At the same distance, the peak pressure was calculated as 6.1 kPa (~1 psi) using the B-S-T method, and it was concluded that the windows could break. Although there are no direct effects on human health, it can be said that injuries due to glass breakage may occur. Software and correlation results were found to be compatible. This is an inherent consequence of the software based on the B-S-T explosion model. In Scenario-2, the largest impact distance of thermal radiation was in the yellow threat zone. The yellow threat zone is less harmful than the orange and red threat zone. The results obtained with the hazardous properties of hydrogen were parallel.
Assessing the role and effectiveness of barriers against hydrogen leaks with QRA (Quantitative Risk Assessment) and calculating the probability of barrier failure for the final consequences can help to reach more realistic conclusions. Combining the results of the researchers' work with the results of this study can provide a more accurate decision-making ability to manage safety risks[26].
Ventilation is one of the simplest and most effective ways to reduce and mitigate gas explosions. Ventilation can help reduce the concentration of flammable gas and relieve explosion overpressure[41]. Explosion suppression materials/structures are of interest to mitigate hydrogen-air cloud explosions in confined spaces. Explosion suppression materials are mesh or porous structures filled into confined containers or channels. With specially designed shapes and dimensions, these structures will reduce flame speed and hydrogen concentration, thus mitigating the explosion effect[42]. Drainage systems should be equipped with water traps to prevent flammable vapors from penetrating the drainage system. Control rooms should be designed to prevent the entry of flammable vapors when there is a risk of exposure to flammable gas. For example, a vapor-tight building with positive internal pressure may be designed to prevent the penetration of a flammable cloud into the building. Maintenance procedures should provide increased oversight of those parts of the plant that contain more reactive flammable liquids and vapors. Operators and maintenance engineers should be briefed on the hazards of explosions as part of process safety training courses[12]. One way to limit the extent of a flammable cloud is to use a vapor fence to contain the cloud. This may have the advantage of limiting the spread of heavier-than-air pancake-shaped clouds. In dense areas, fuel gas sensors can be installed to give dangerous flammable clouds the needed size. Careful consideration should also be given to the exact use of trees and vegetation around the site, limiting their width to less than 2 m. When designing new facilities, attention should be paid to separating congested areas to limit flame acceleration. Empty buildings located near or within process units may have a collapsible wall to prevent high overpressures from building up inside the building. This can prevent the transition of an external flammable cloud to a high-velocity jet of ignition and possible explosion[15].
-
In this study, a consequence analysis was conducted for hydrogen fuel cell production facilities. Consequence analysis was performed using ALOHA software and the B-S-T method. A case study was conducted in a hydrogen fuel cell production facility in Türkiye for the first time. Accident scenarios were developed on a vertical cylindrical tank storing hydrogen at high pressure. Jet fire and non-fire as a result of release cases were analyzed due to a rupture in the pipe connection to the tank bottom. The most considerable distances were determined for the flammable vapor cloud area in the hydrogen release scenario without fire (> 300 m). This was followed by the vapor cloud explosion area developed under the same scenario at a distance of approximately 200 m. In this way, the hazardous properties of hydrogen were supported. Depending on the scenario, the changing impact areas and affected structures were shown on Google Earth. It was determined that domino effects could occur inside and outside the facility. It was observed that windows and surrounding buildings could break in the establishment, and injuries could occur due to glass breakage. The B-S-T method and the ALOHA software obtained similar results for explosion effects. The ALOHA software is currently based on the B-S-T method with minor modifications, and this situation was confirmed once again with the calculations. It has been shown once again that the consequences of industrial accidents are often large-scale and dangerous, and it has been seen that preparing scenario-based emergency plans is extremely important. In addition, it has been shown that using geographic information system sources such as Google Earth effectively interprets the effects and vulnerability of a possible accident. In the relevant facilities, different accident scenarios can be developed with the changes in hydrogen storage tank specifications, chemical amount, operating conditions, and atmospheric conditions. These scenarios can be modeled, and effective emergency plans can be prepared by evaluating the effects of fire, explosion, and toxic release.
-
The author confirms sole responsible to the following: study conception and design, manuscript preparation, data collection and analysis, etc.
-
All data generated or analyzed during this study are included in this published article.
-
I want to thank Beyza Akbas for her contribution to the study.
-
The author declares that there is no conflict of interest.
- Copyright: © 2024 by the author(s). Published by Maximum Academic Press on behalf of Nanjing Tech University. This article is an open access article distributed under Creative Commons Attribution License (CC BY 4.0), visit https://creativecommons.org/licenses/by/4.0/.
-
About this article
Cite this article
Cetinyokus S. 2024. Determination of possible industrial accident effects on a hydrogen storage tank in a fuel cell production facility. Emergency Management Science and Technology 4: e020 doi: 10.48130/emst-0024-0020
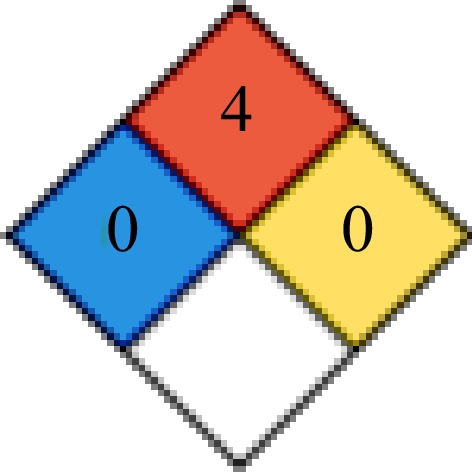